Digital and physical prototyping blends design, engineering, and iterative experimentation to bring ideas to life.
In this page, you’ll find a collection of my personal prototyping work
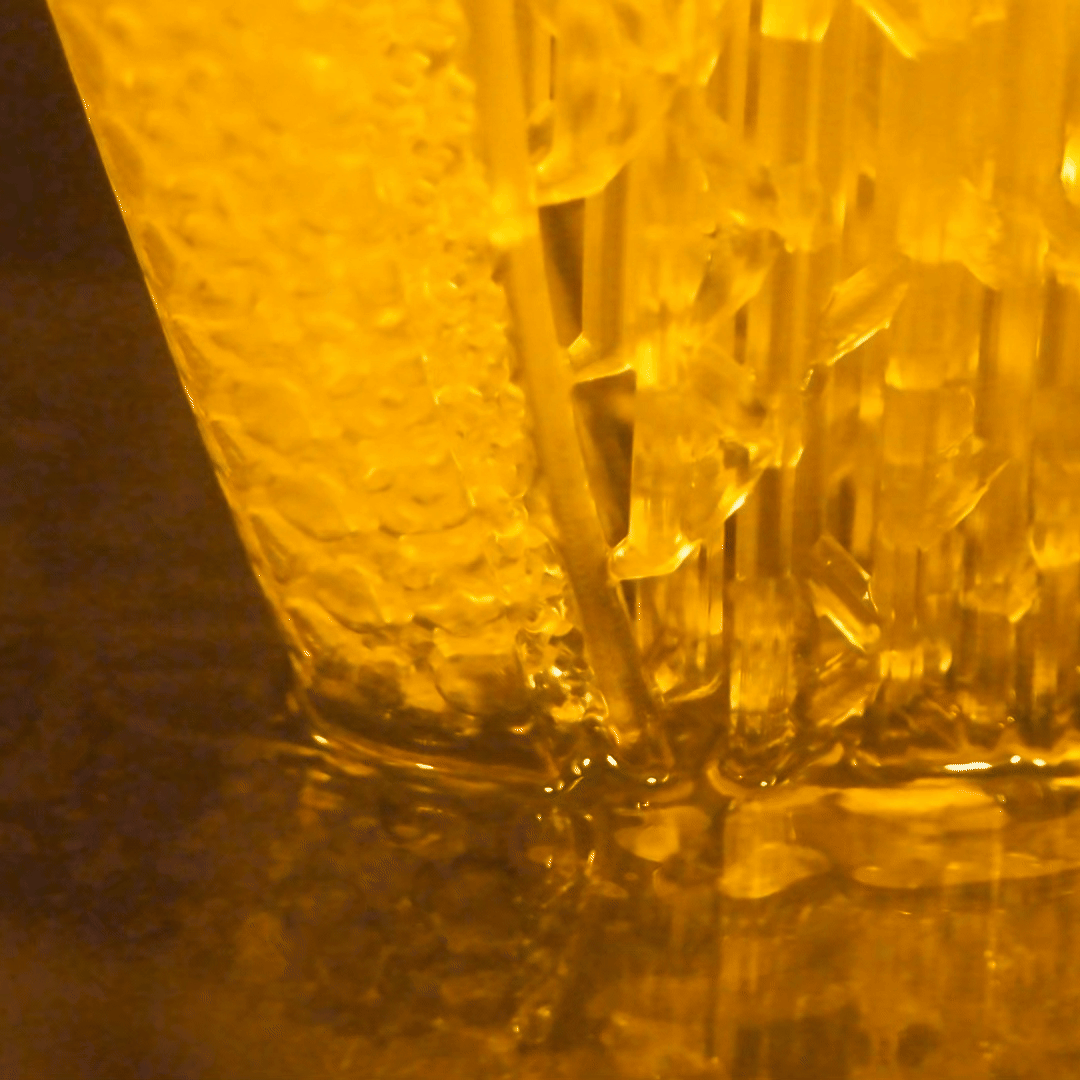
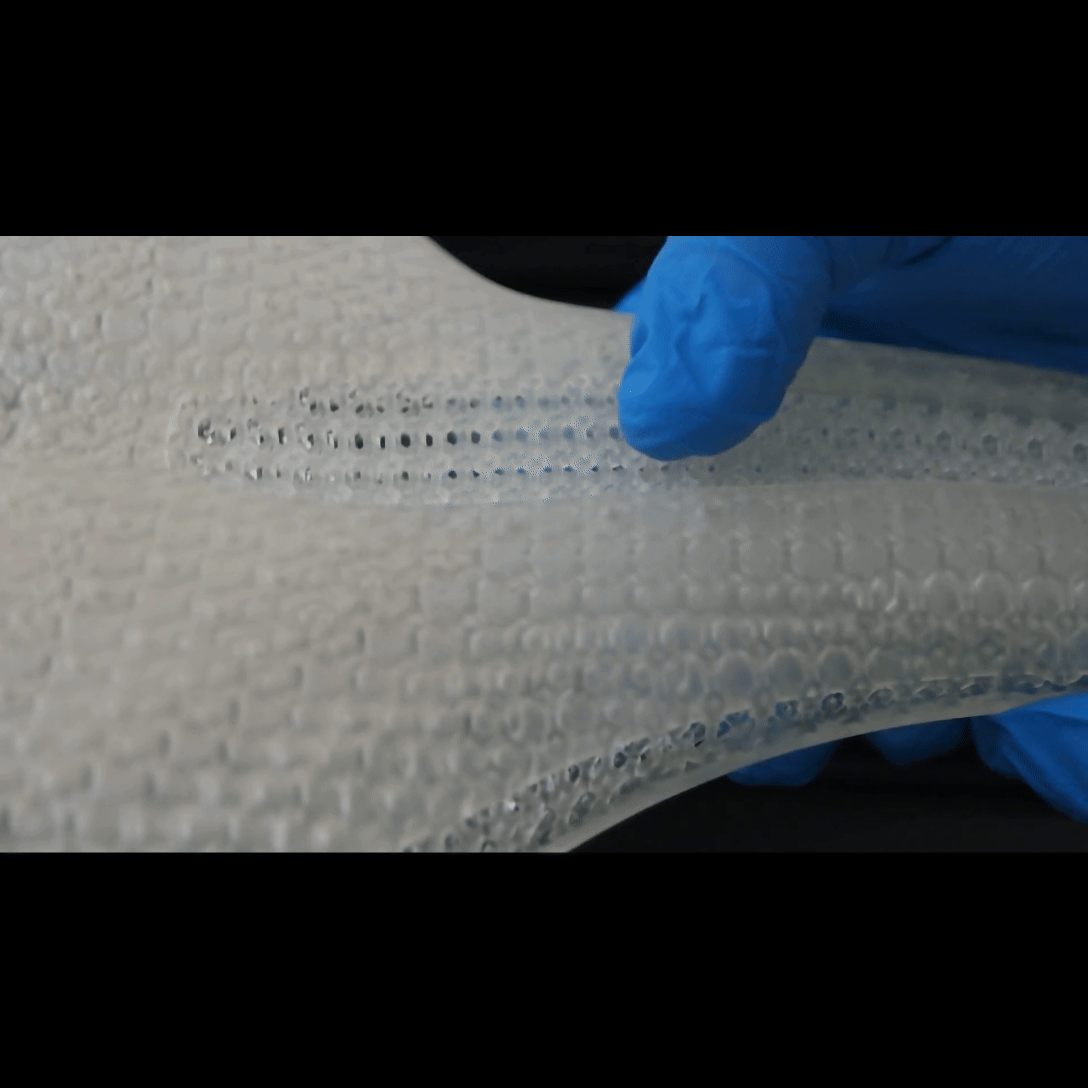
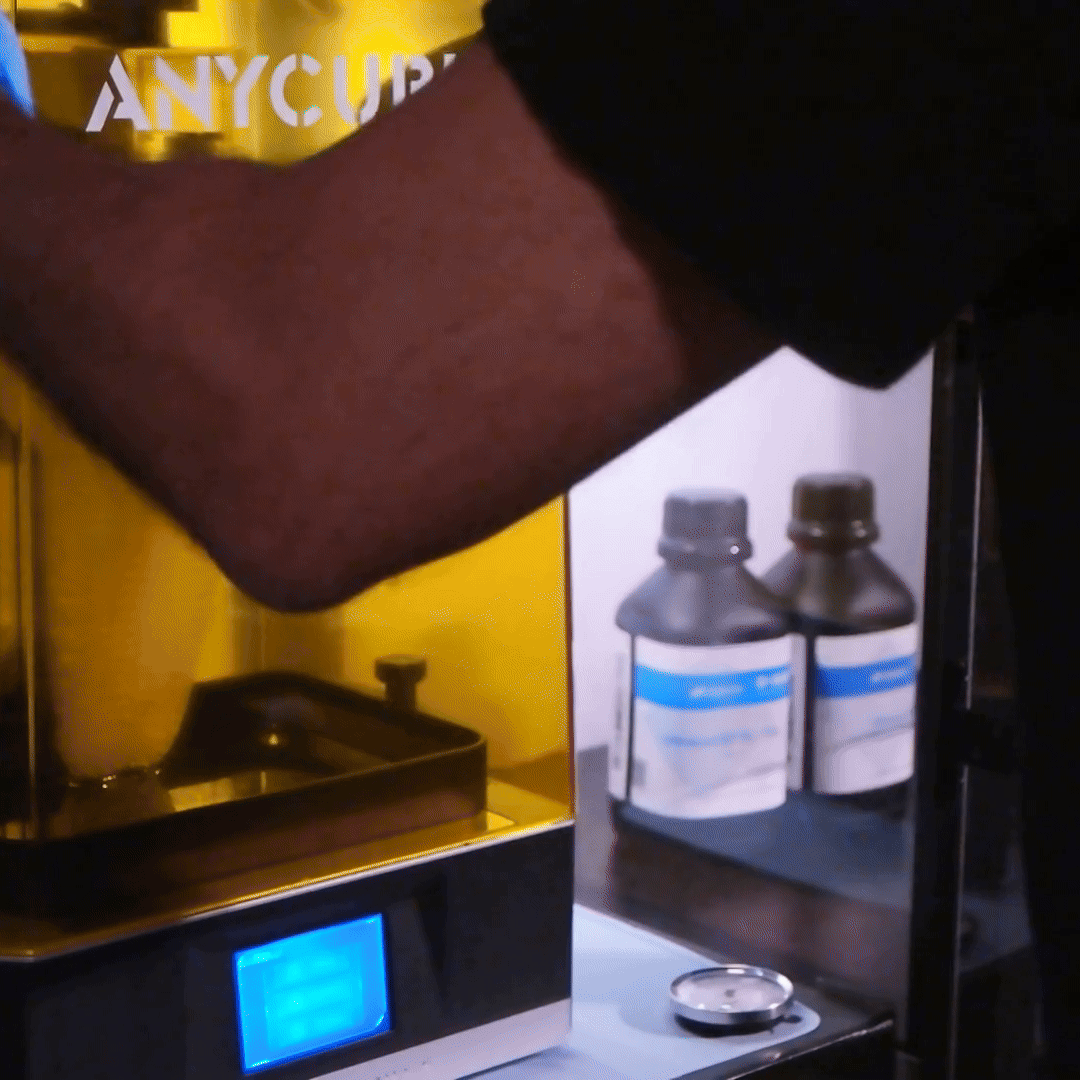
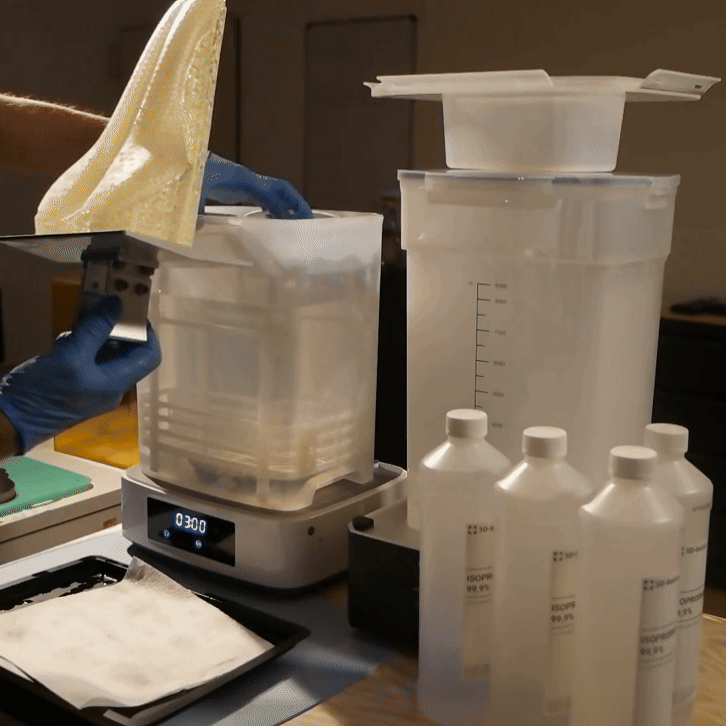
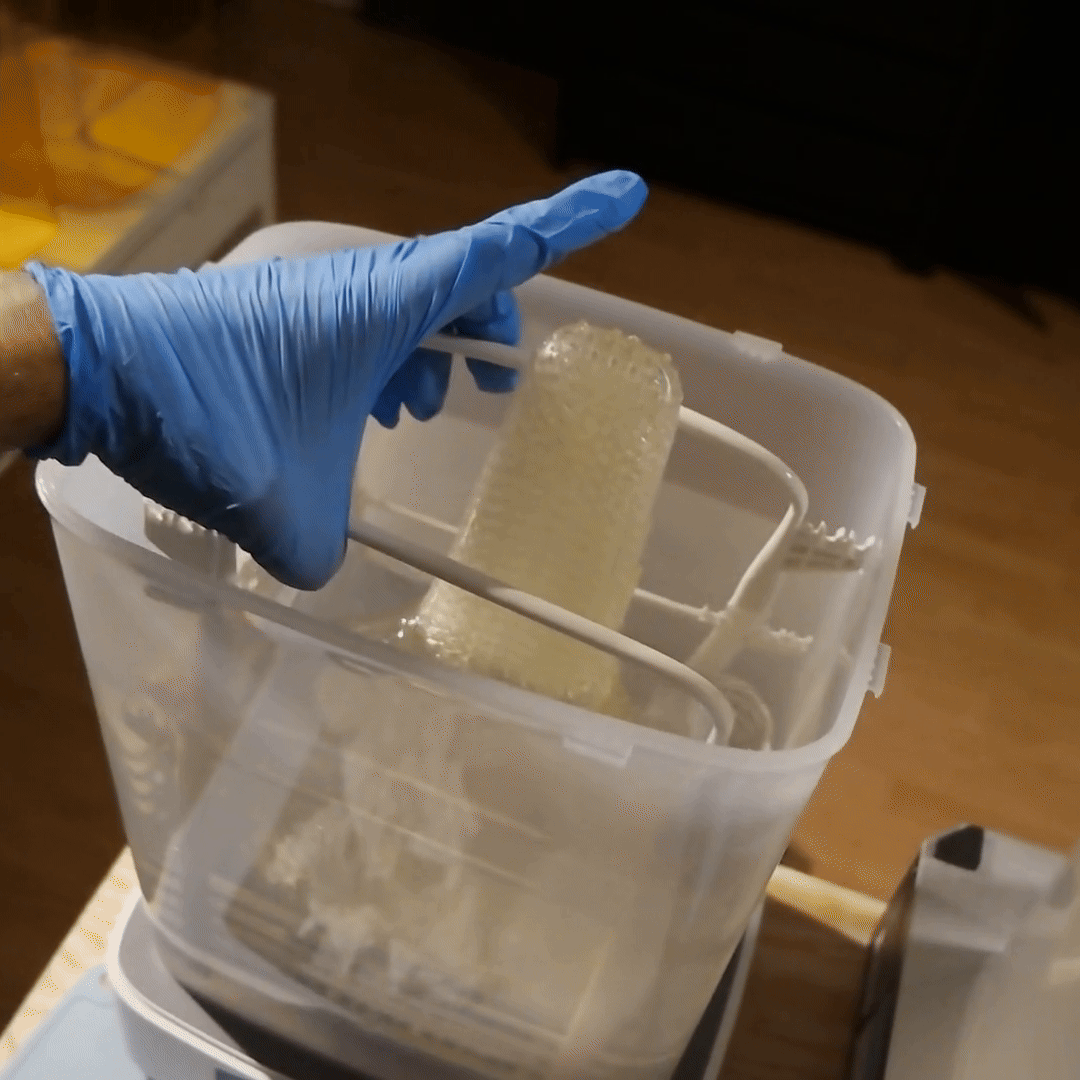
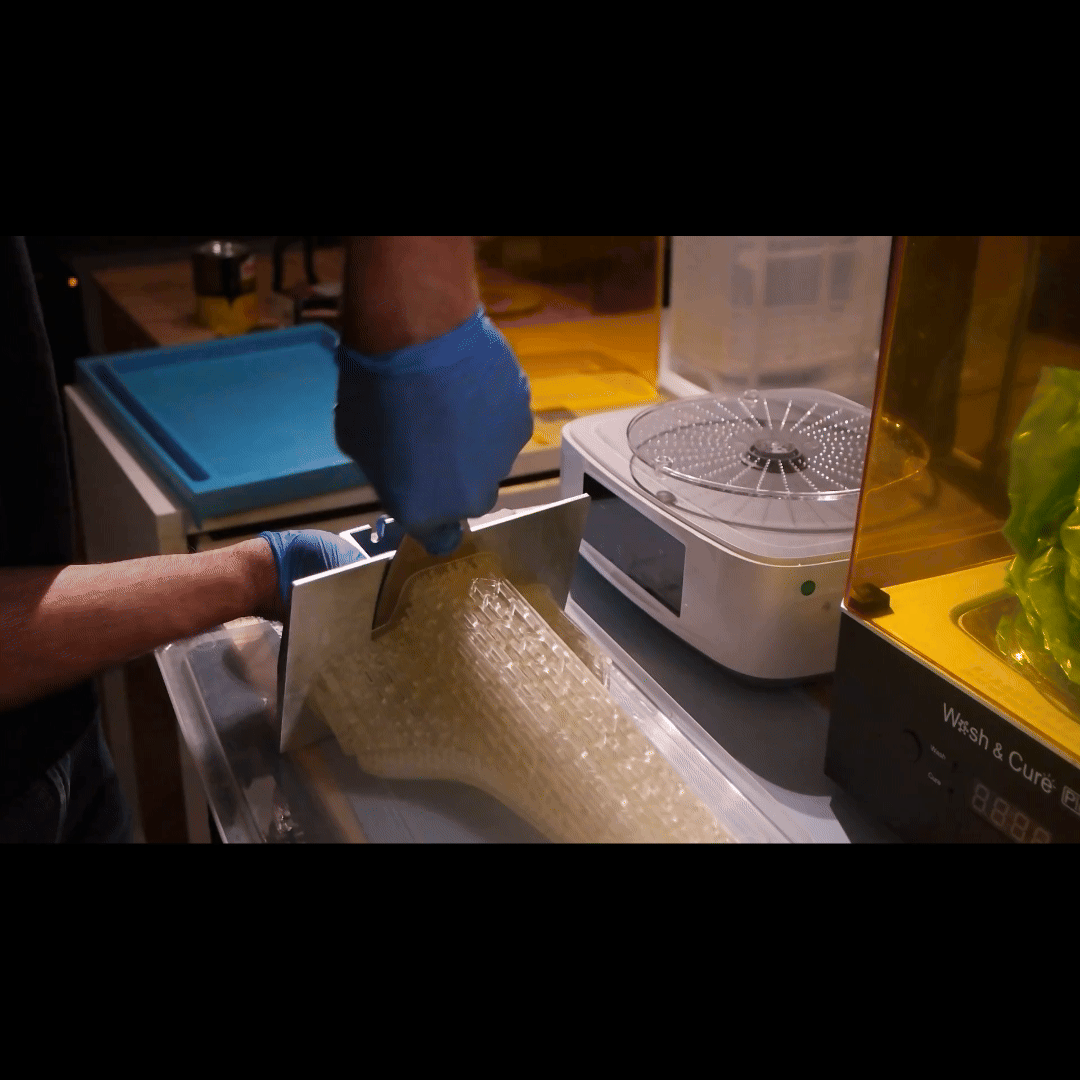
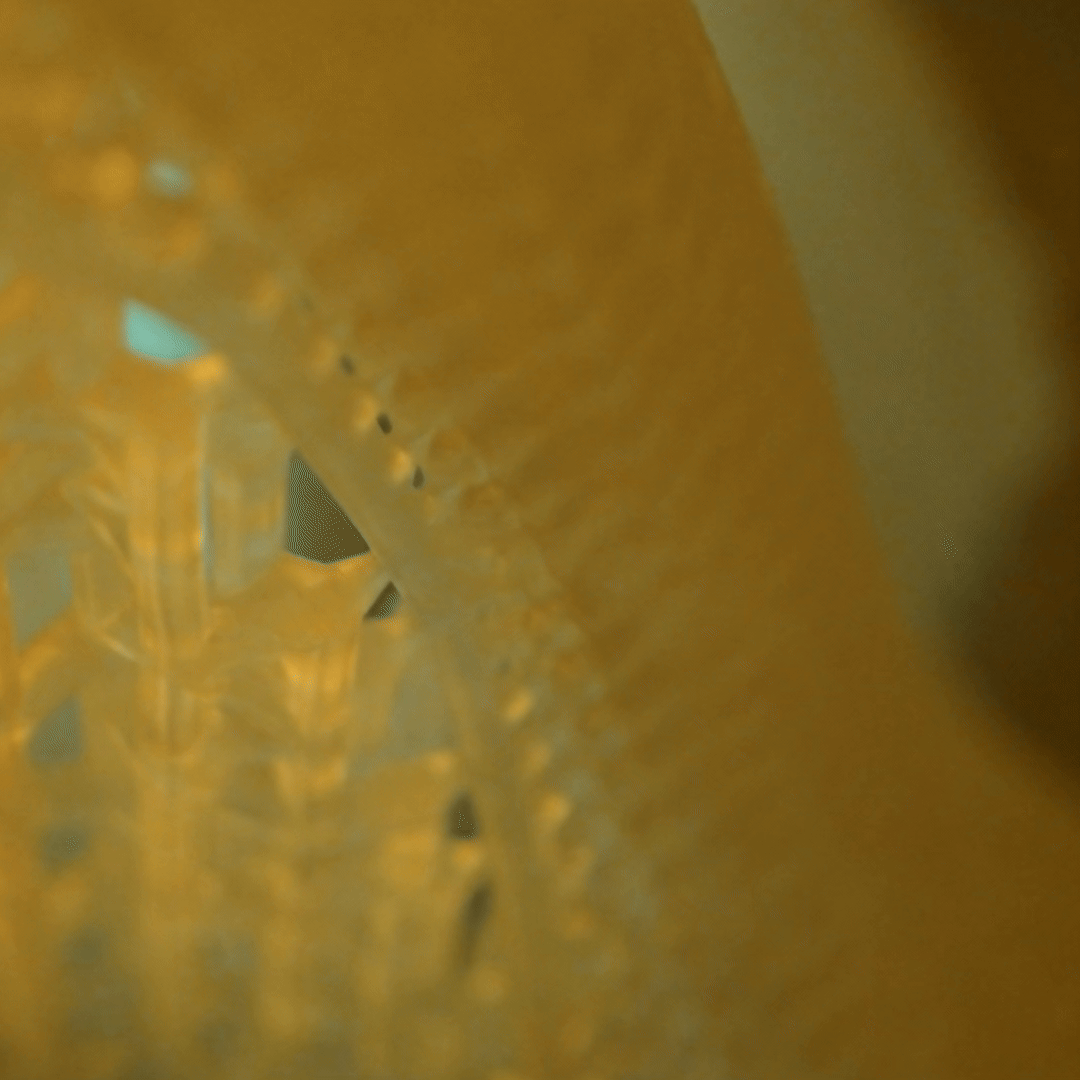
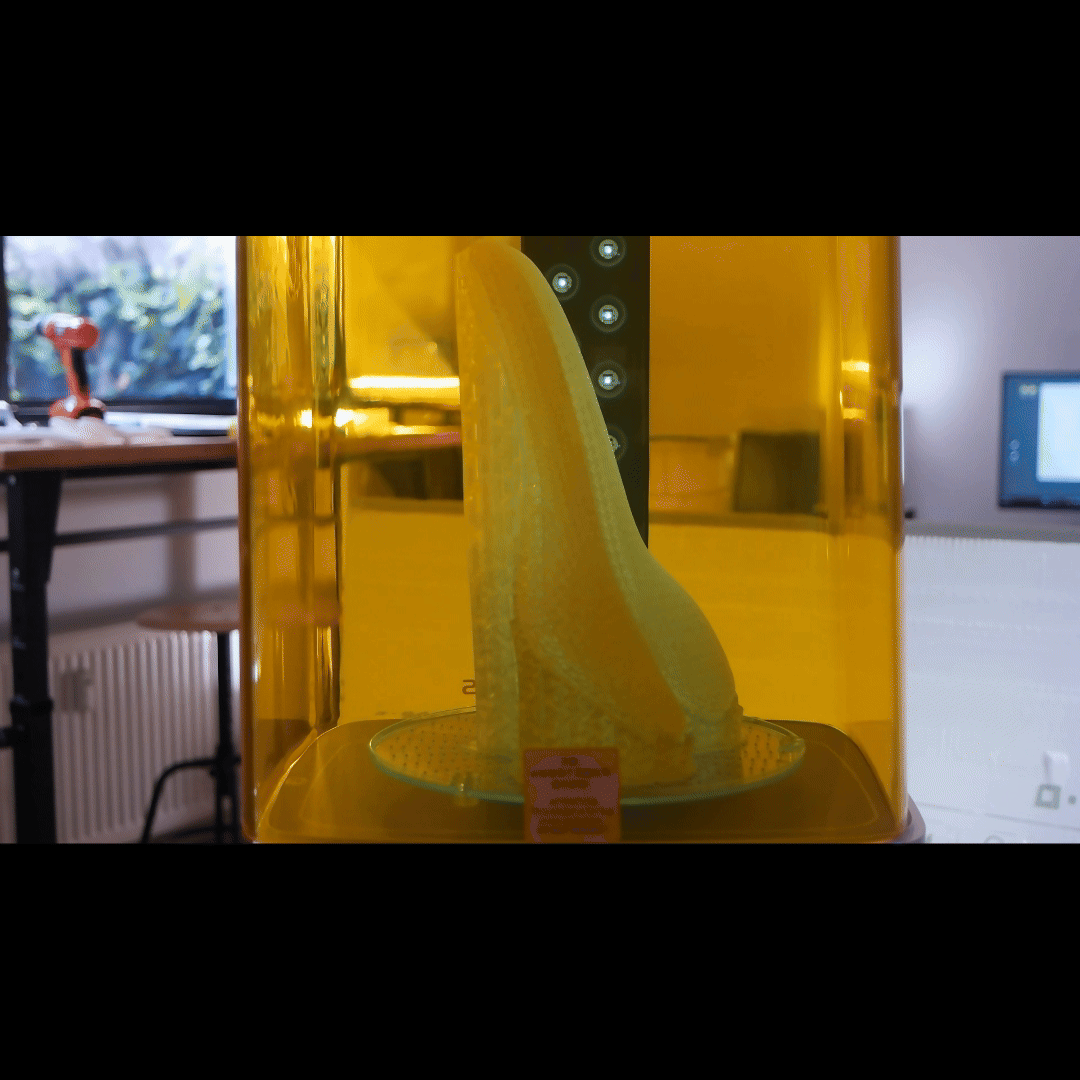
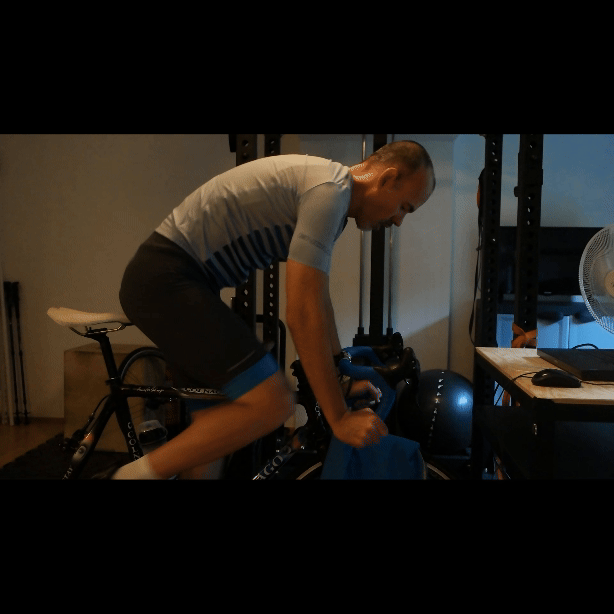
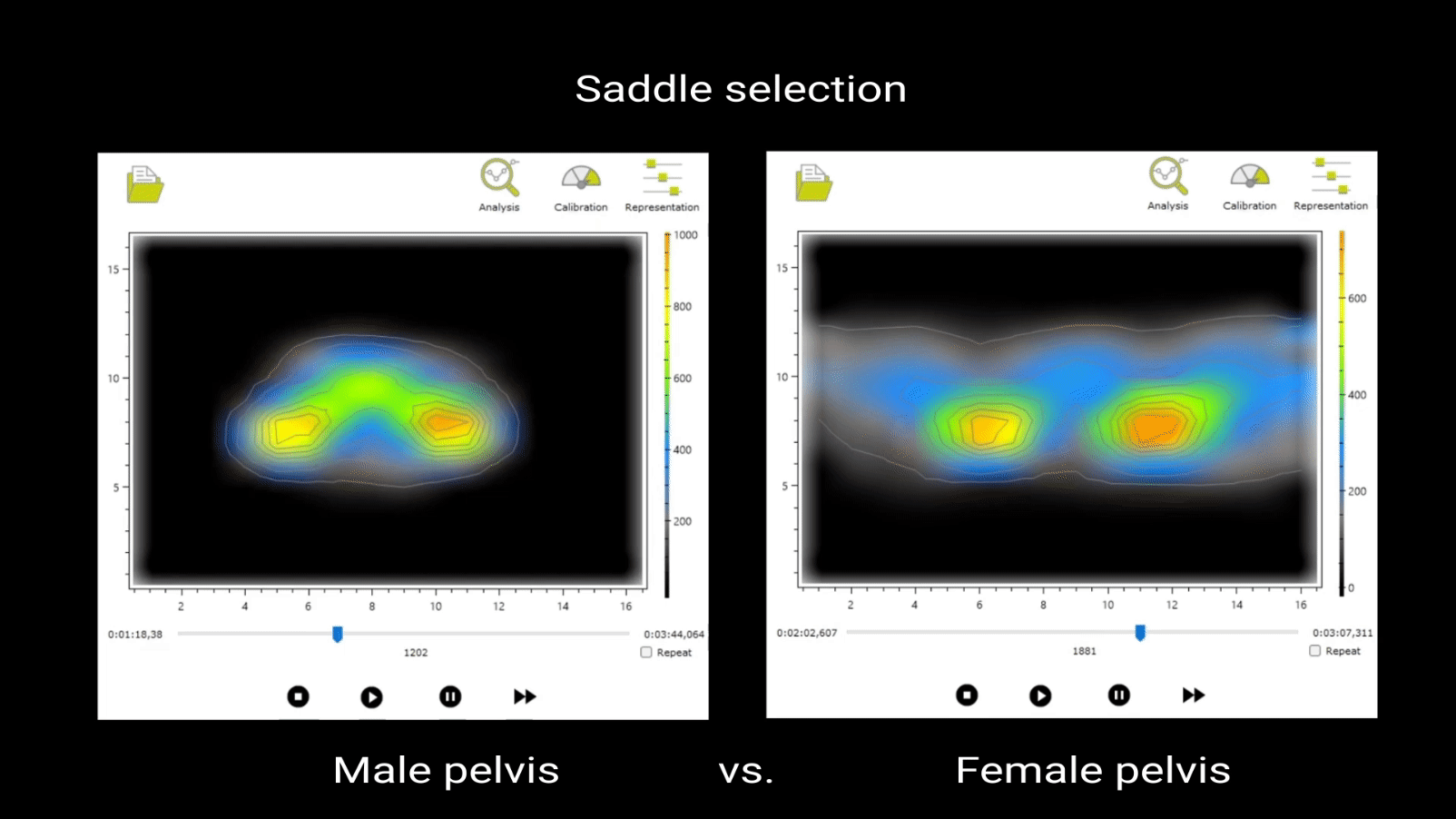
Product design and development through learn by doing approach
I enjoy the freedom to research, experiment, and adopt multiple roles to create products that make a positive impact on people’s lives.
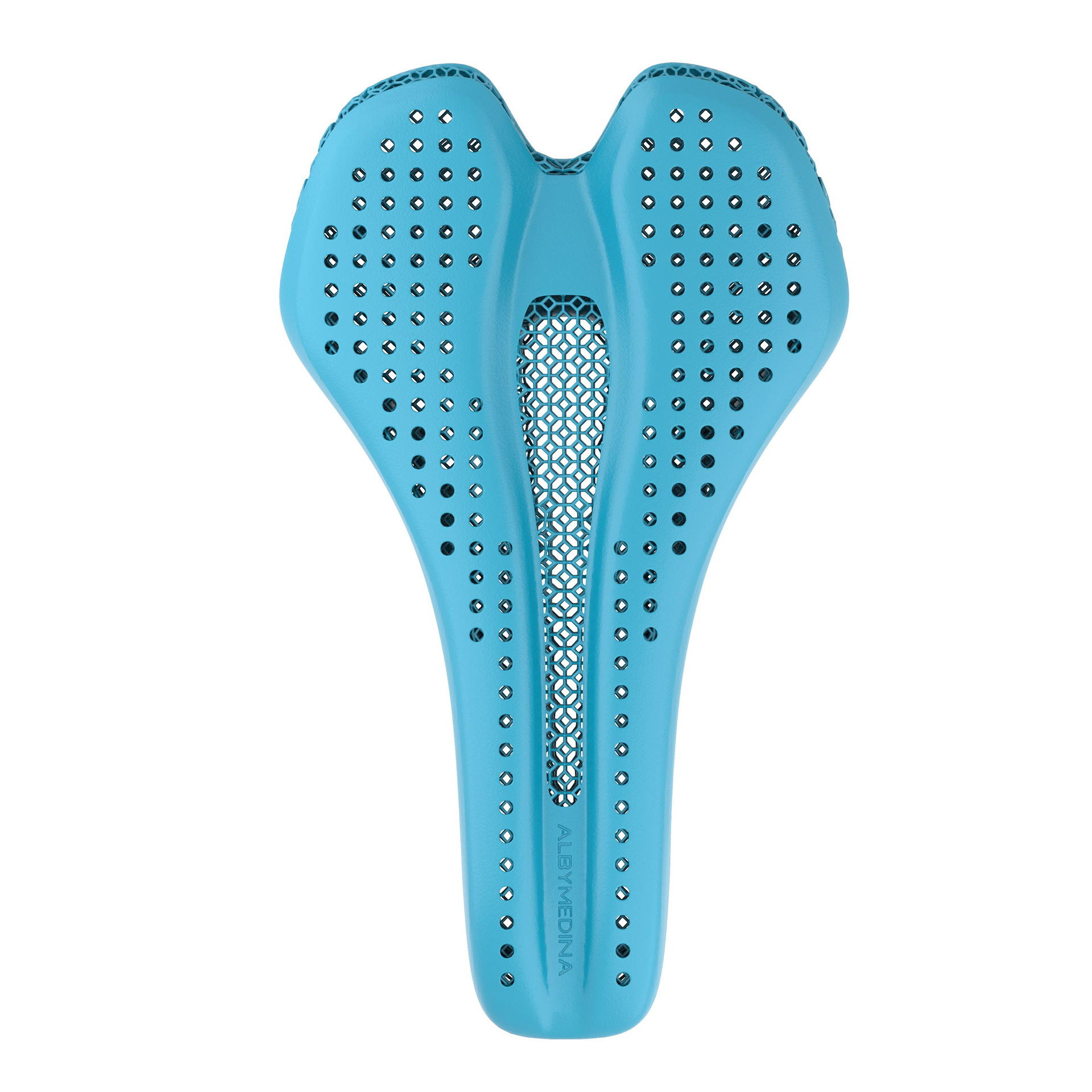
Functional 3d Lattice paddings
I explored solutions for riding in extremely wet and harsh environments, with high presence of moisture and exposure to salty water. To address this, I developed an integrated drainage system that improves water and airflow, offers strong mechanical resistance, and enhances pressure dissipation along the saddle’s central longitudinal axis—particularly beneficial during stationary seated pedaling. The configuration of the shell-to-padding interface allows for the use of thin, firm padding without compromising comfort or safety.
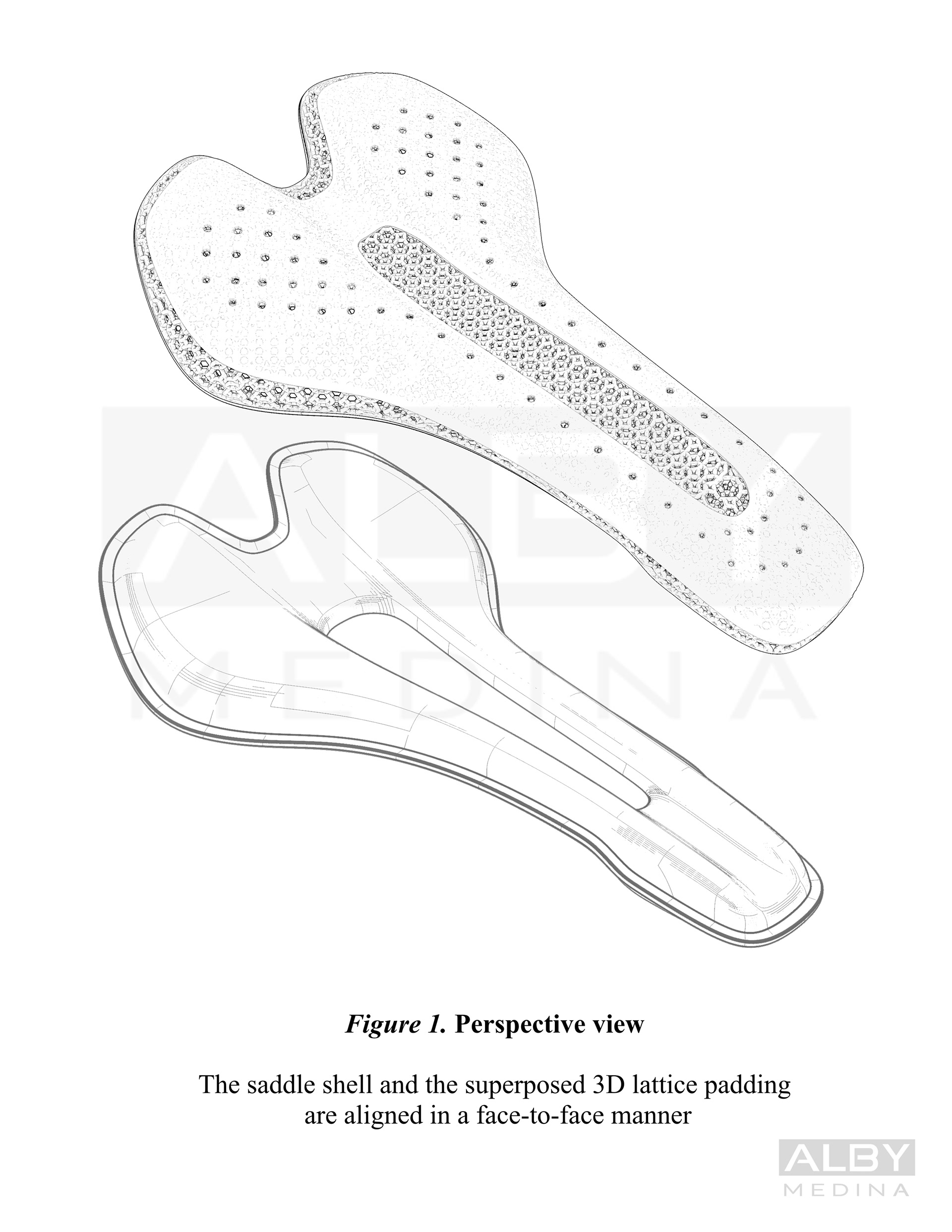
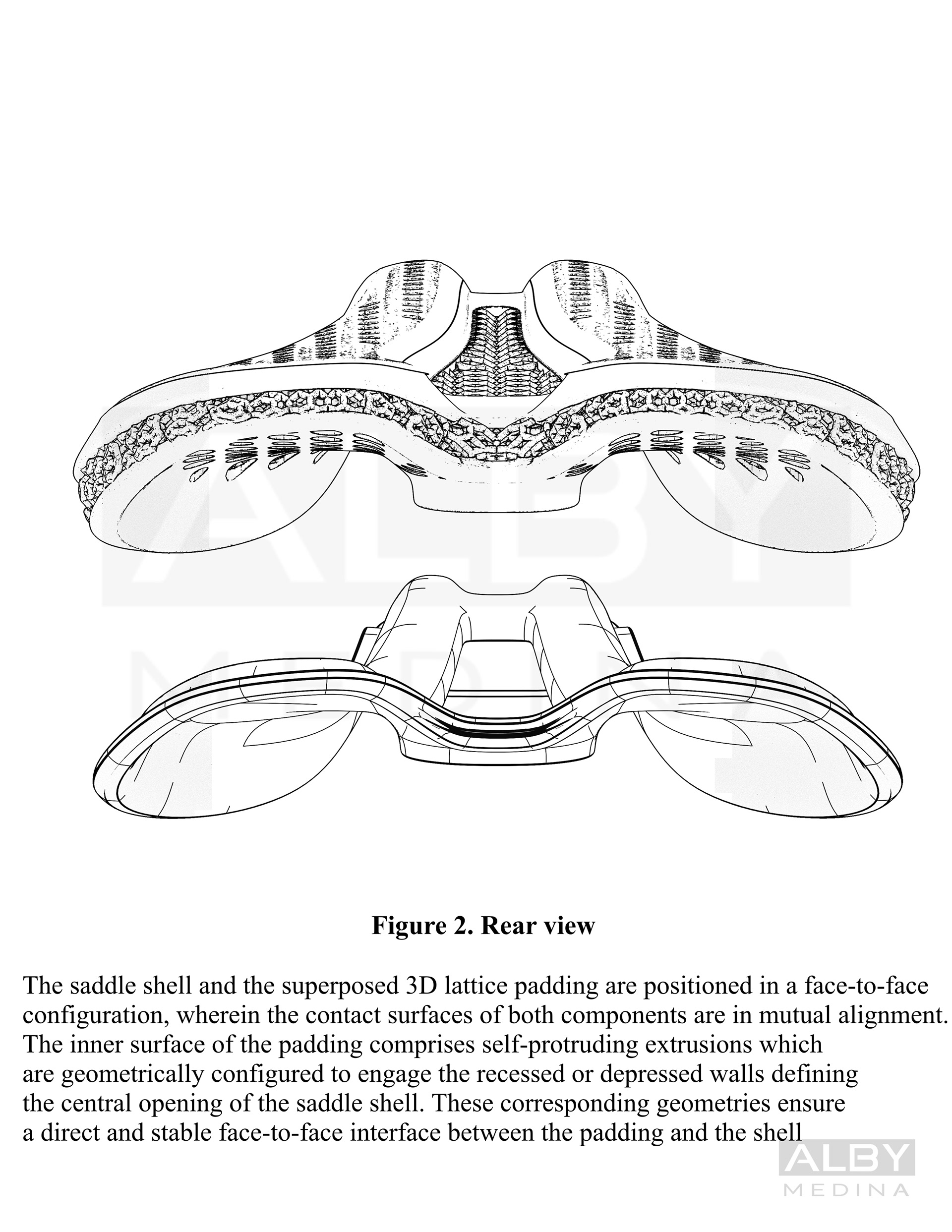
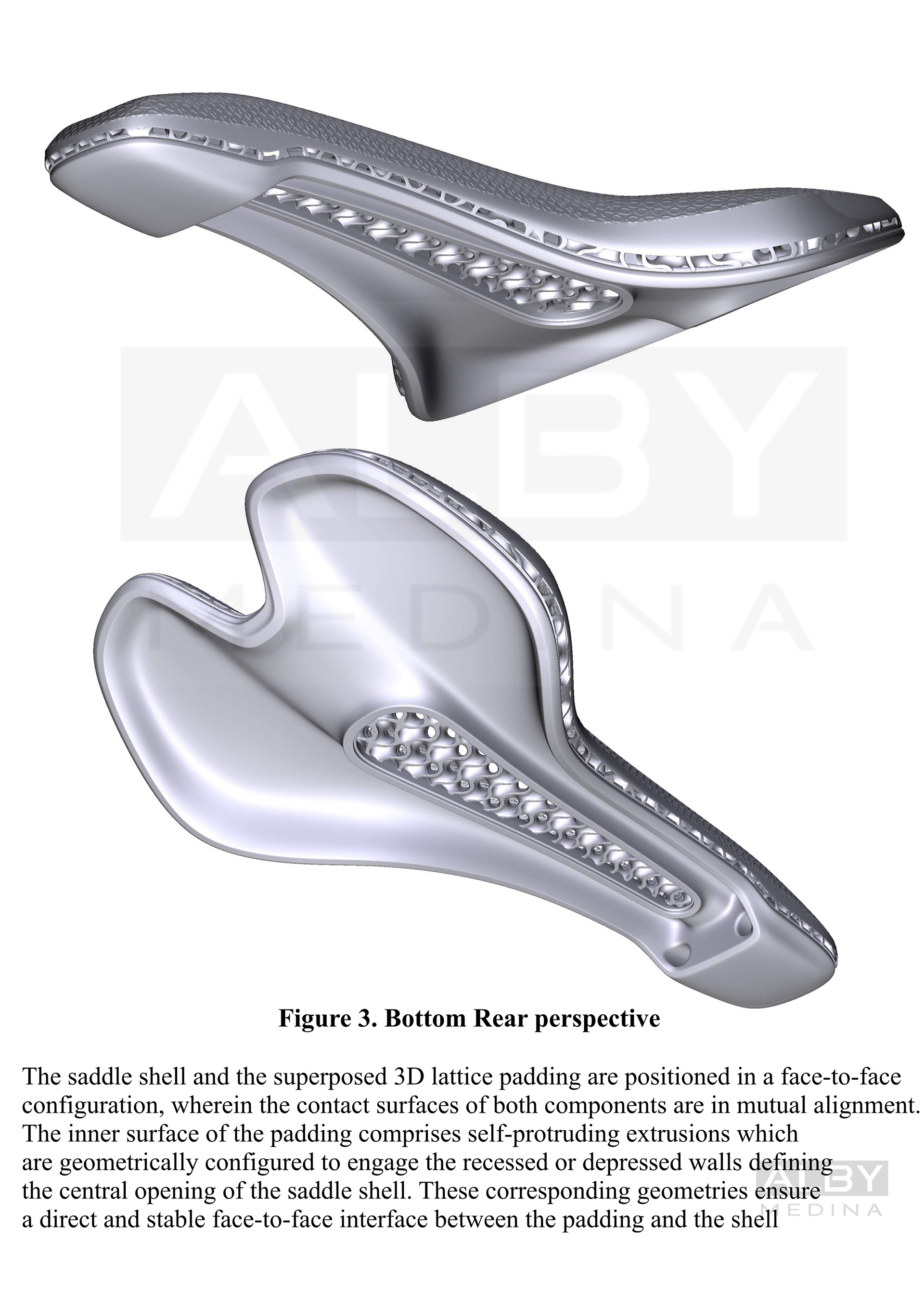
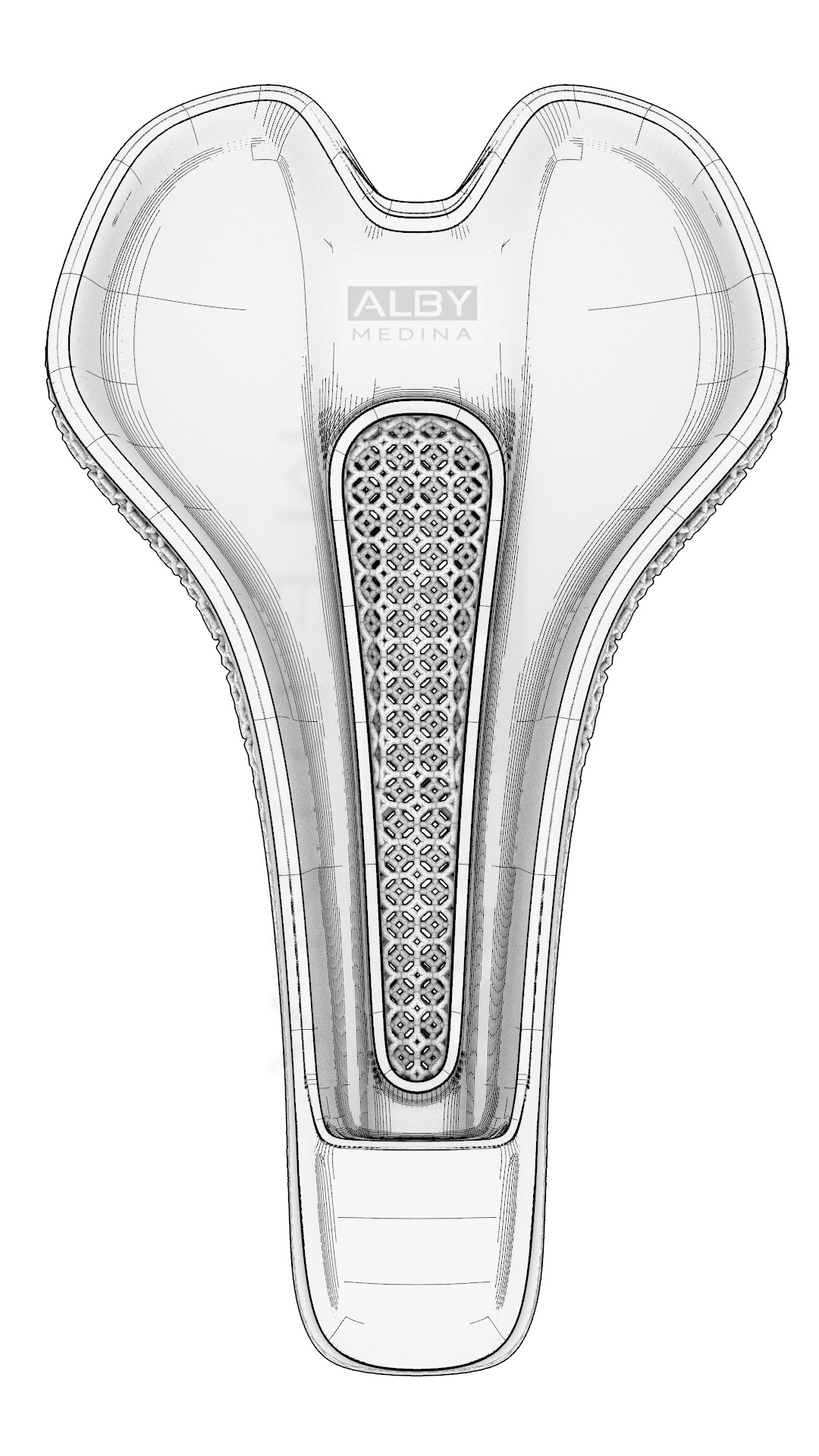
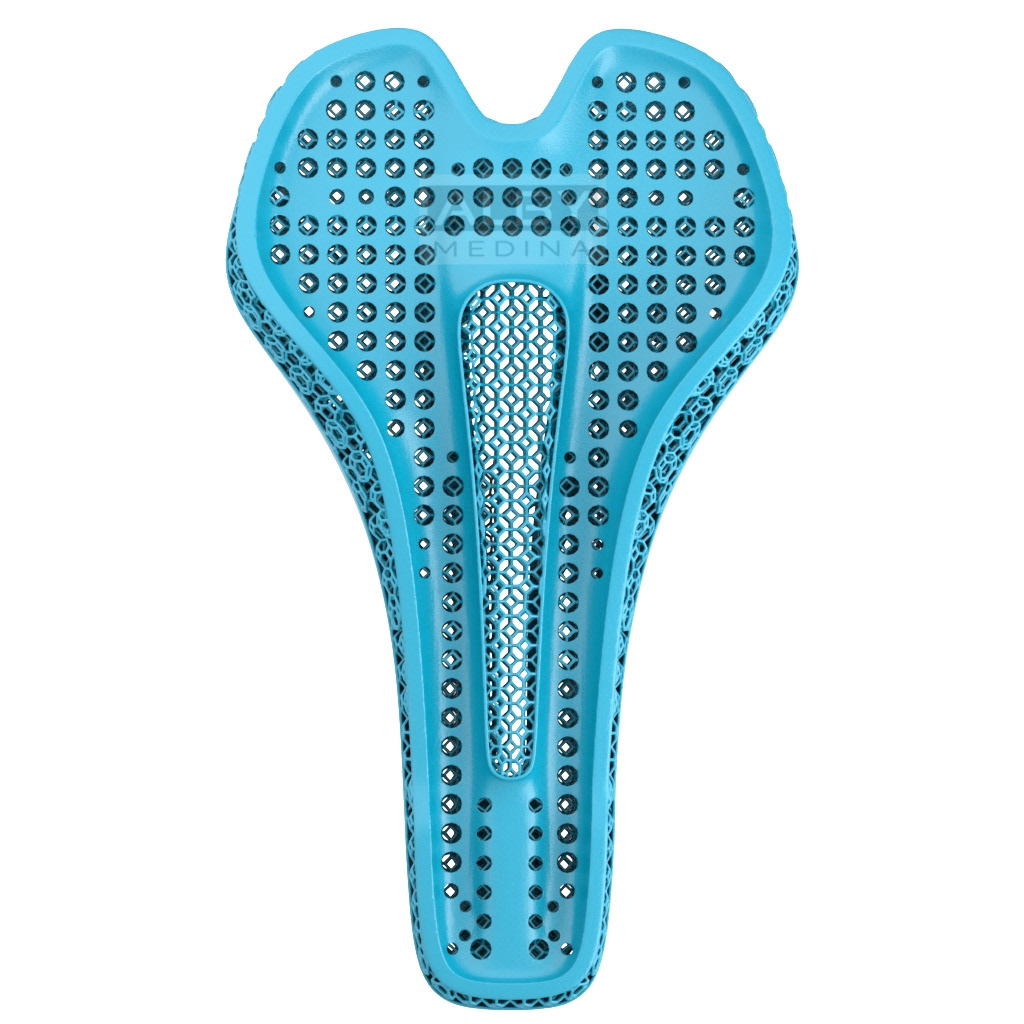
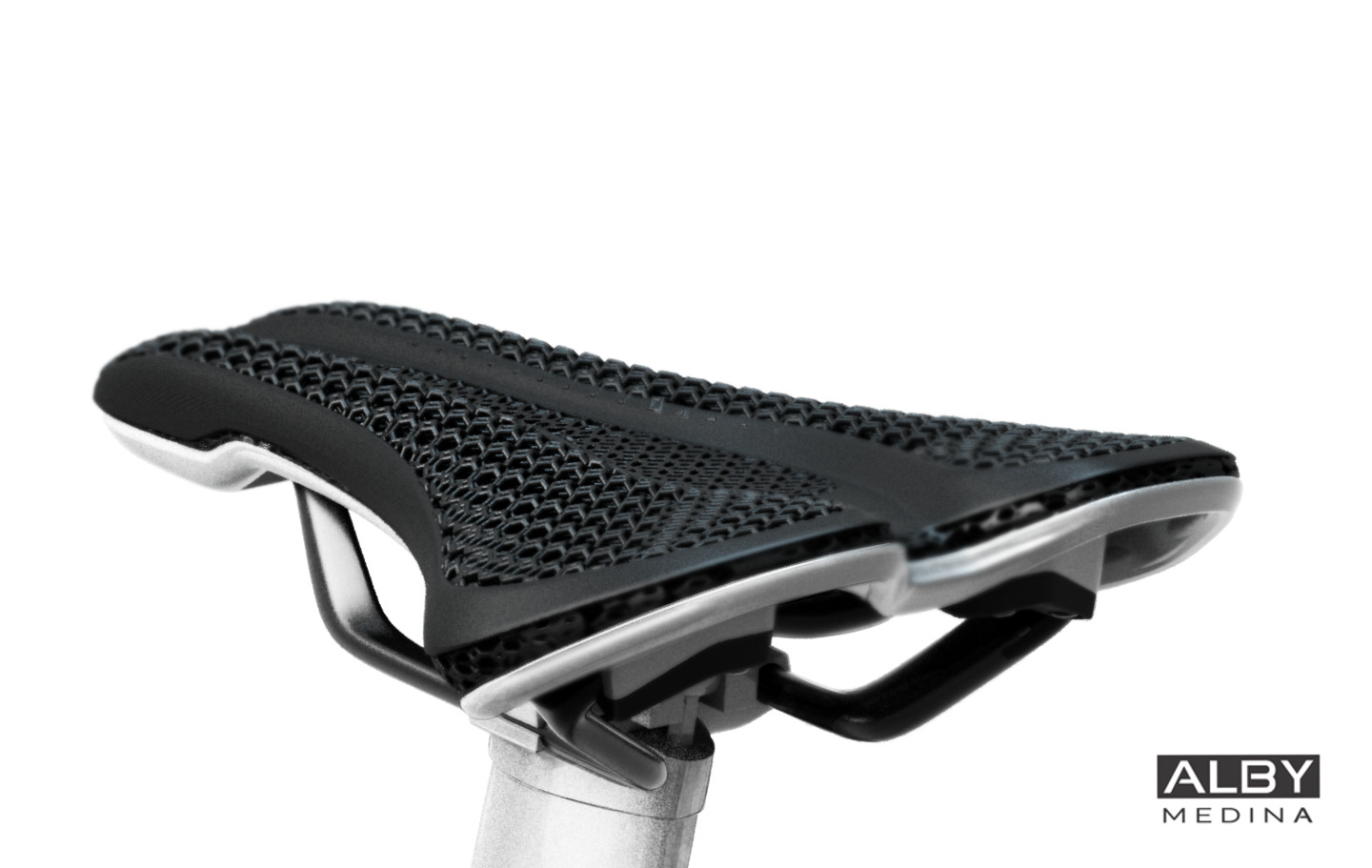
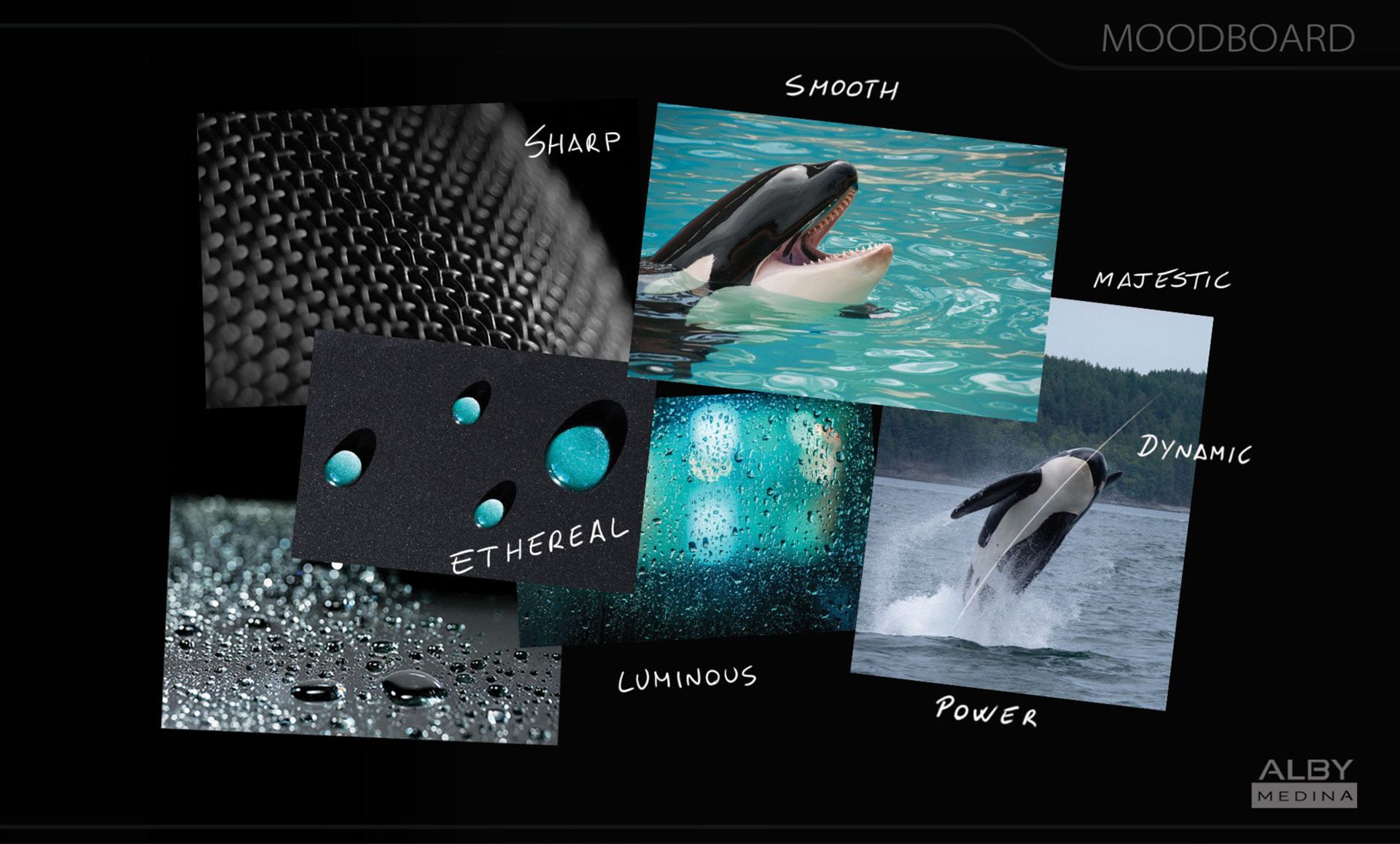
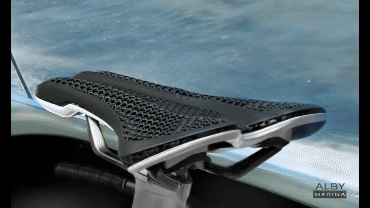
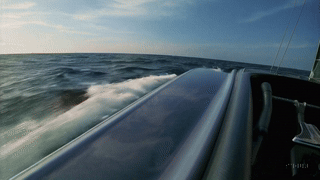
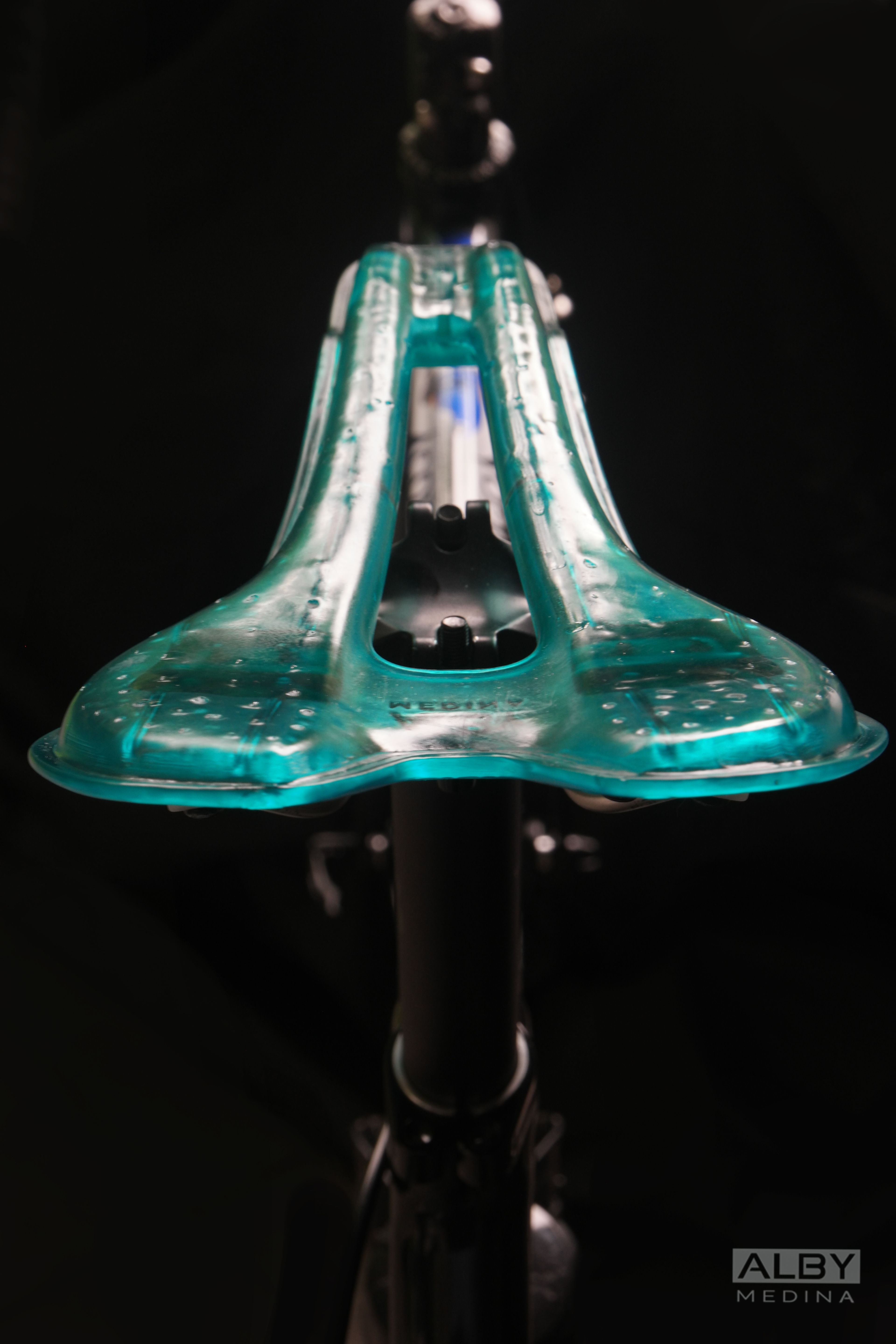
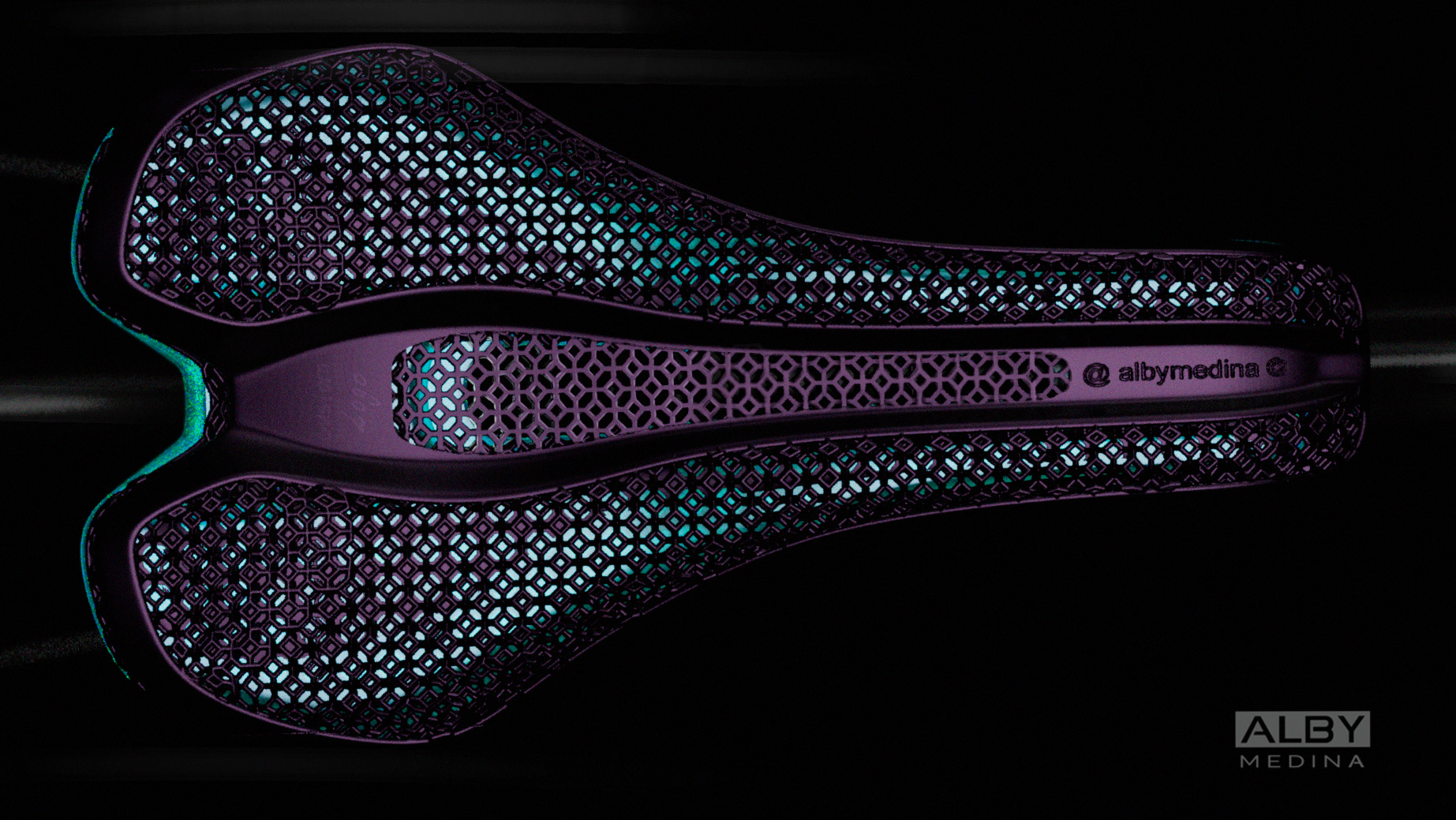
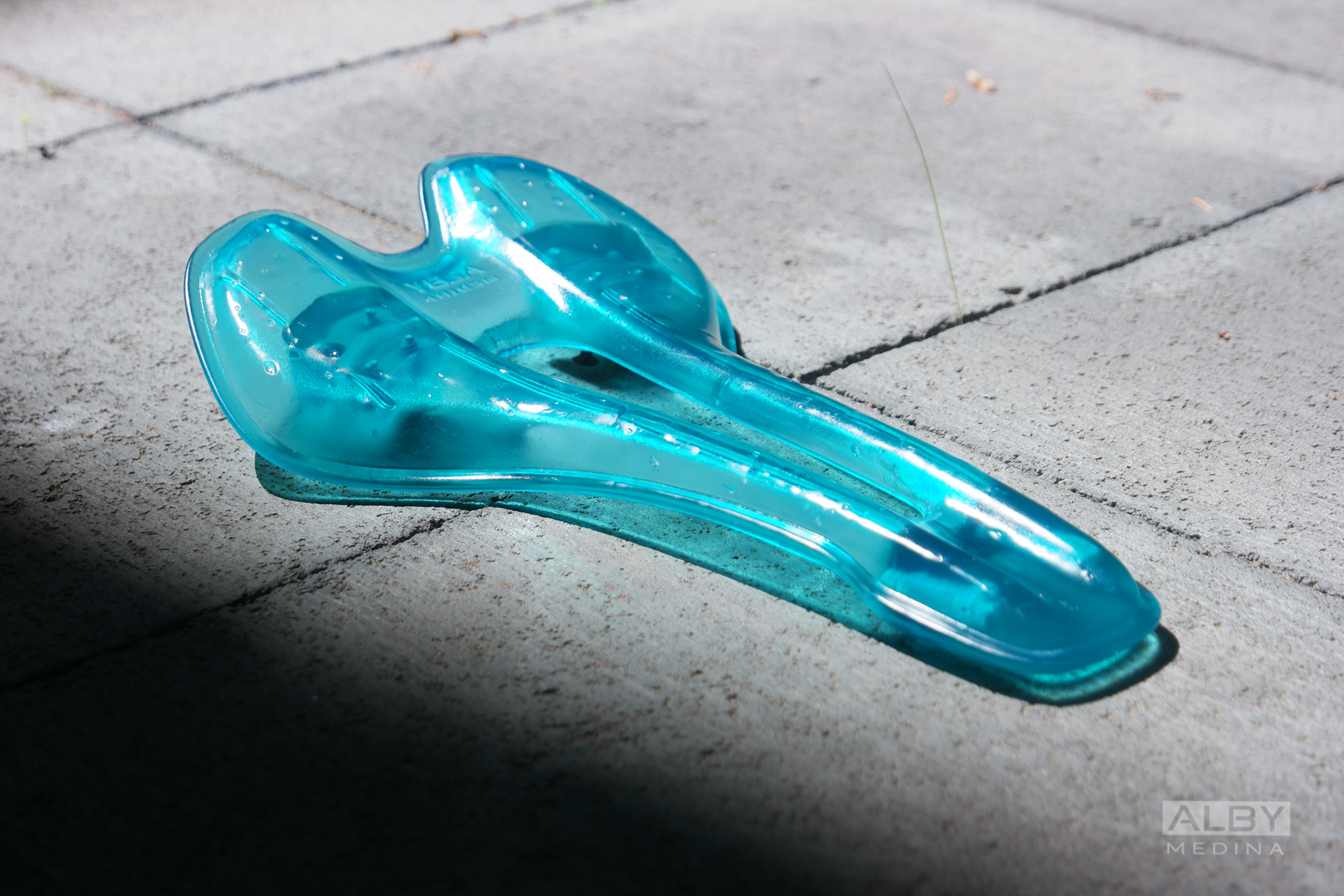
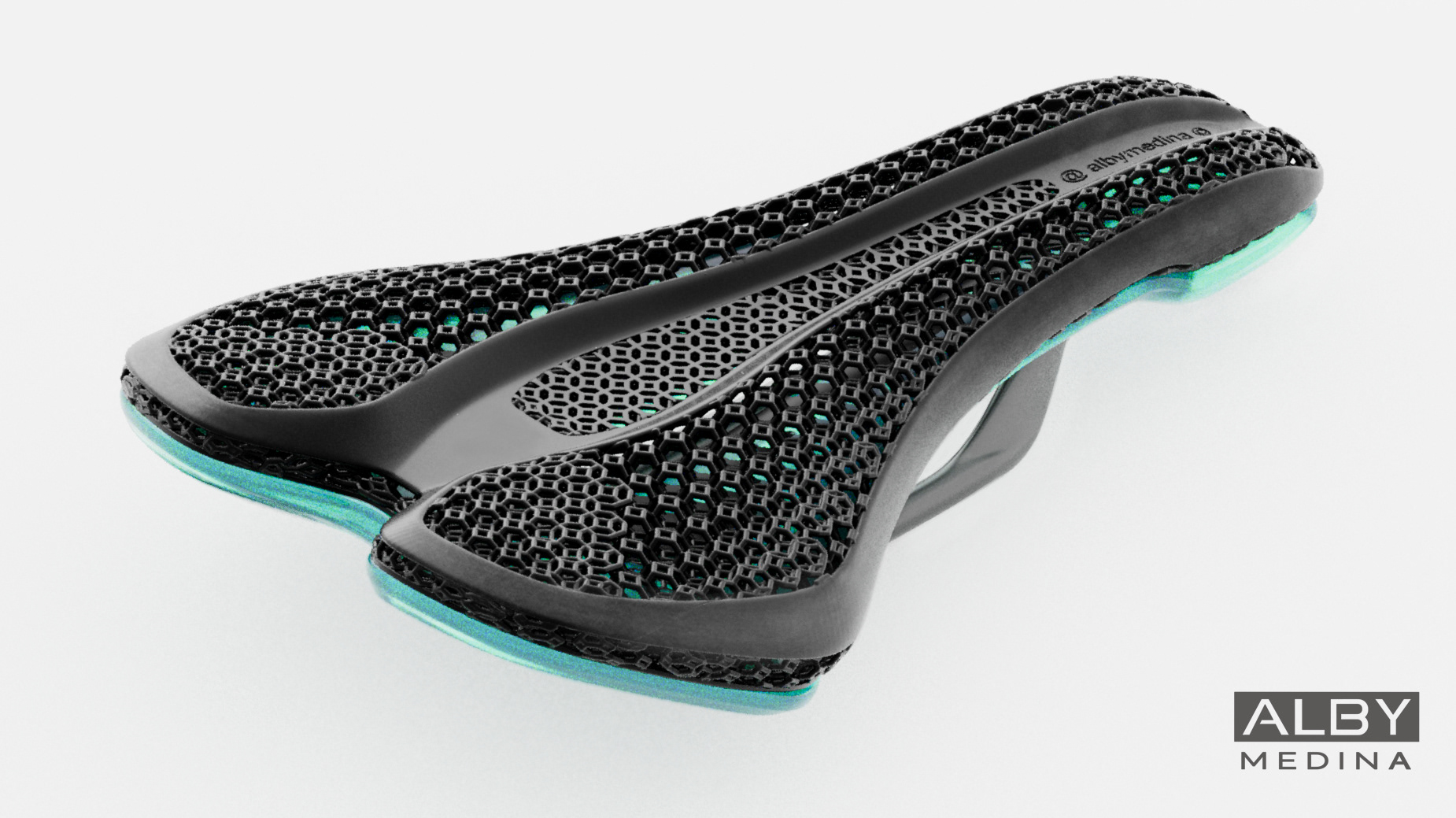
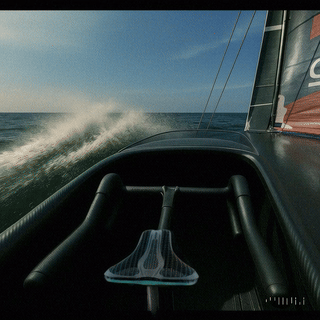
Material studies
The product is intended to perform at high-moisture environments with exposure to sweat and saltwater.
I developed prototypes using MSLA, Powder Bed Fusion (PBF), and Powder Bed Laser Fusion (PBLF).
The product is intended to perform at high-moisture environments with exposure to sweat and saltwater.
I developed prototypes using MSLA, Powder Bed Fusion (PBF), and Powder Bed Laser Fusion (PBLF).
Materials included elastomeric photopolymers, TPU based, polyamides, and Titanium Ti6Al4V. I explored DFAM and material science to understand structural performance and compatibility. Material behavior was also studied testing different types of lattice structures and configurations. I also had to consider material selection based on resources available.
In so called "developed countries", additive manufacturing is often viewed as a promising path forward, but it isn’t always the most cost-effective or sustainable option, and particularly, in countries where hype and marketing are the only means to justify hyper inflated prices.
Exploration on Metal Printing. Discussion
Overinflated pricing, logistics, and IP monopolization aside, we now have the tools to create more complex forms with less material waste.
Back in 2021, during my master’s thesis, I looked into metal AM for aero rail frames. In 2024, a short visit to Formnext (Frankfurt) and a conversation with a design company specialized in SLM, based in Barakaldo (Basque Country, Spain), brought the idea back. I started thinking seriously about combining shell frame and rail into a monobloc saddle, with optimized geometry perforations included.
Monobloc parts are no secret, but they need to be done, tested, and iterated to push new ideas. I realized that even small individuals with no corporate ties can still create and invent, maybe because we’ve got high risk tolerance, nothing to lose, and a lot of fun to have.
This remains a hobby project, so I focus first on feasibility and safety. Solve the problem, provide comfort—then think about making it lighter, faster, and sleeker.
Titanium frame designs were hollow, around 65g each, with variable thickness (1.8 mm to 1 mm). Parts were printed vertically with batch production in mind. Print orientation, heat exposure, and surface finishing all have major effects on strength and durability.
Right now, bent titanium, stainless steel, and carbon fiber rails are still the most reliable options. But monobloc designs open the door to more compact, optimized, high performance parts, if done right.
As for worst case scenarios, what happens if the rails break on a turbo trainer, or worse, on the road? It’s a fair and serious concern. A sudden saddle failure could have fatal implications, especially under high load or speed. That’s why early testing must be slow, controlled, and conservative. Then, make it nice.
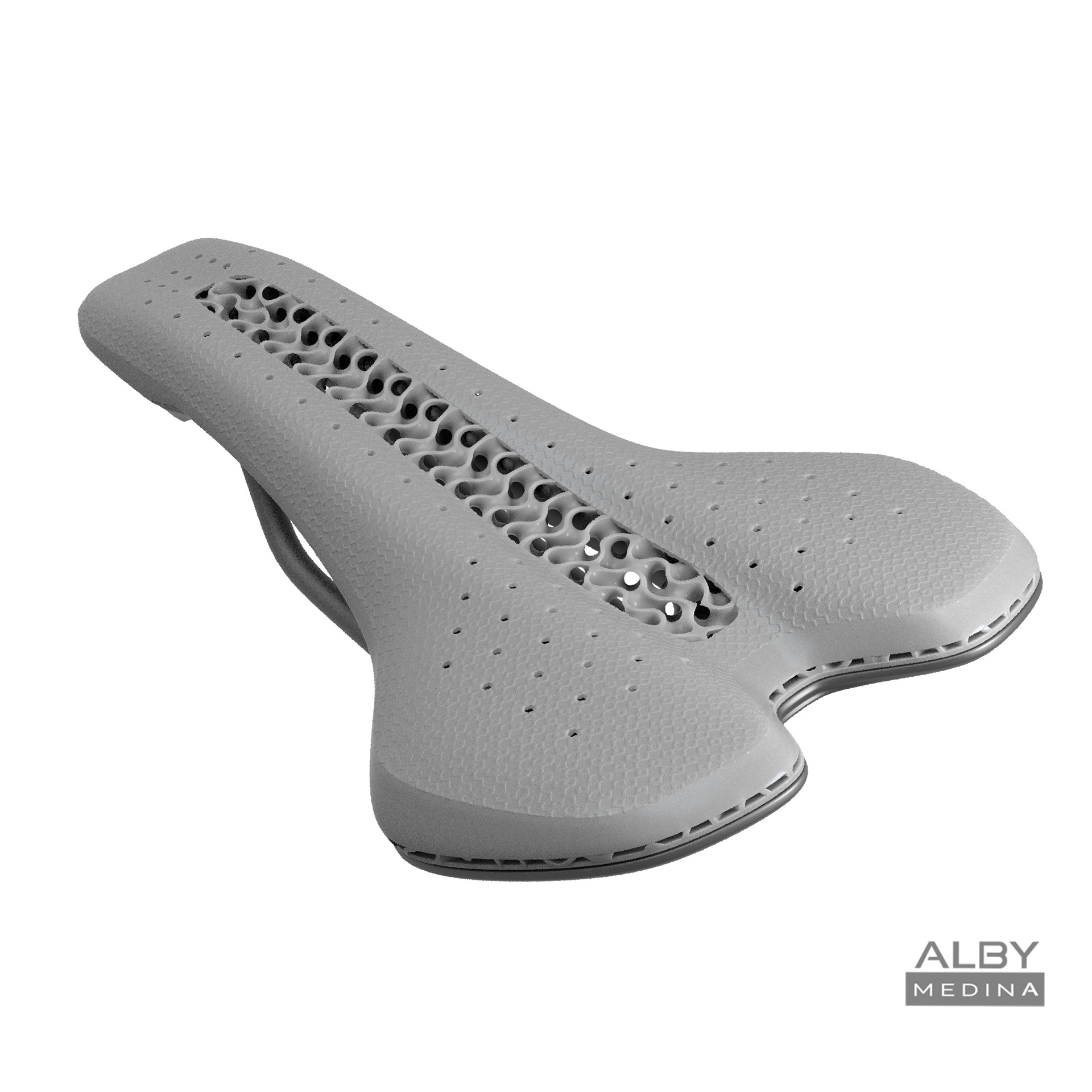
Image description. Gyroid design variant, 80% print-ready. Lattice orientation in the central groove ensures grip without causing bib short wear. Printed in a silicone-like resin with an organic, tactile feel (55–65 Shore A hardness).
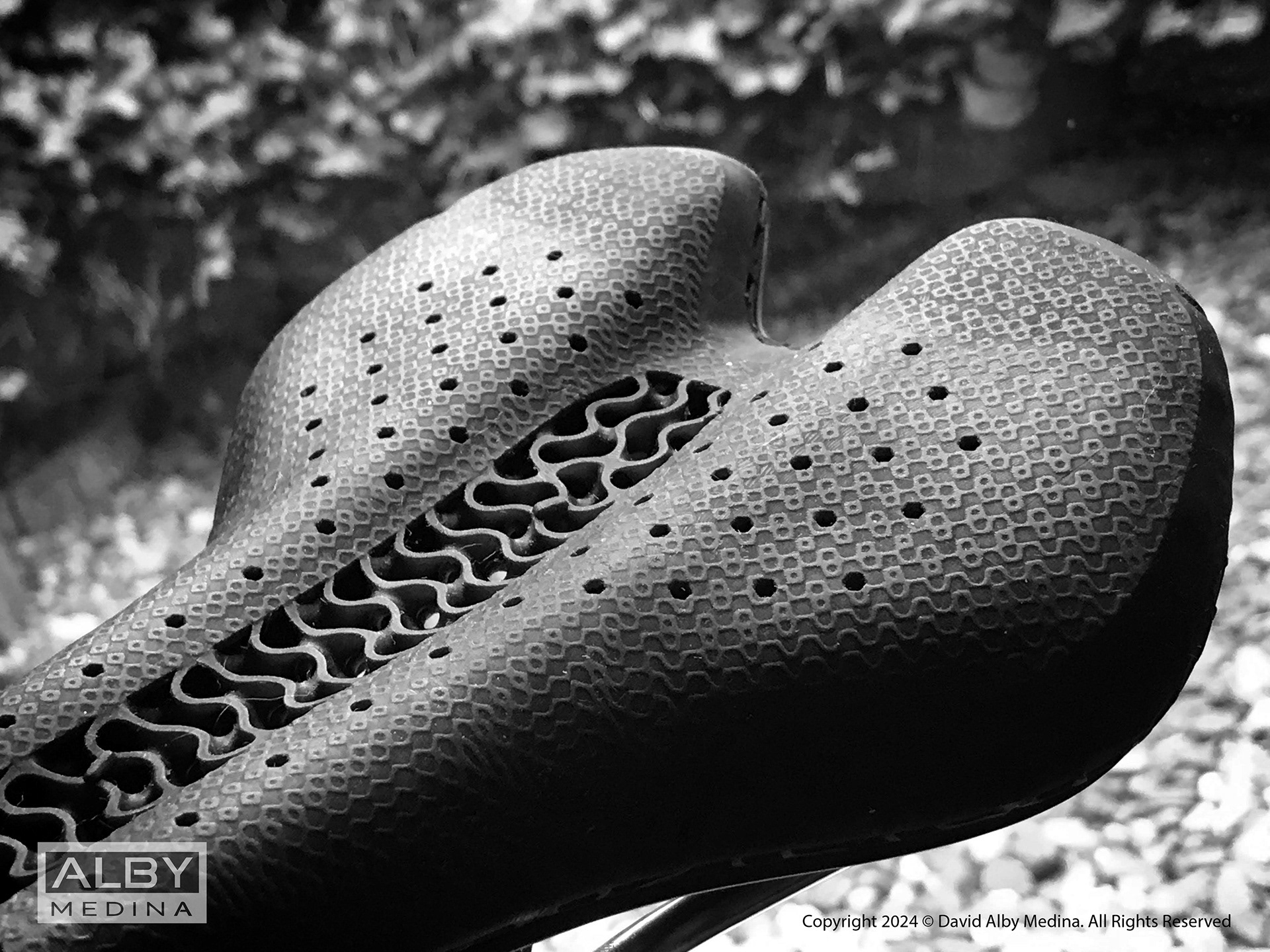
Gyroid foam prototype using flexible photopolymer resin (60 Shore A hardness). Applied minimal printing supports for reliable print.
Organic Function
Much like in nature, organic tissues flow, breathe, and perform beneath the surface of the skin
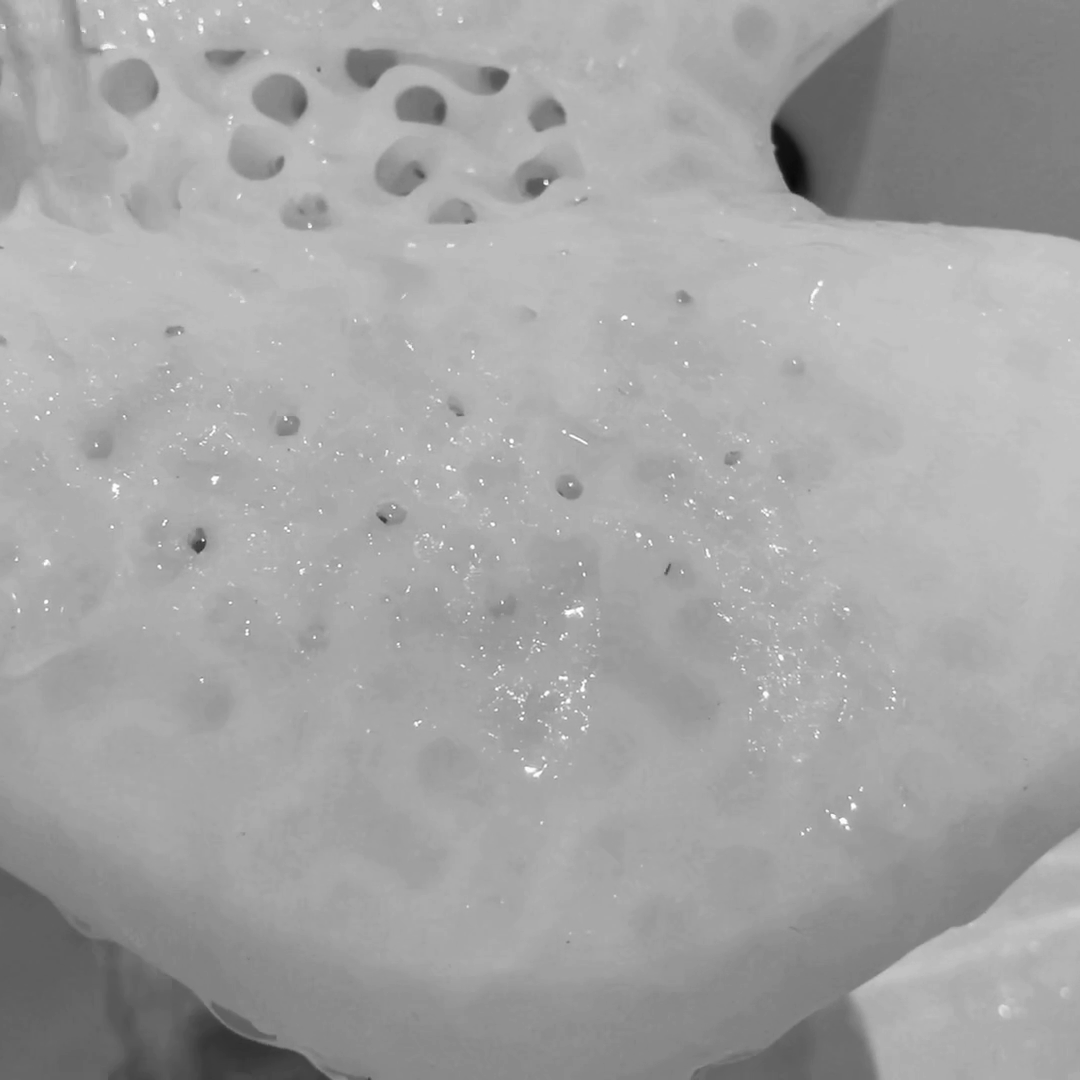
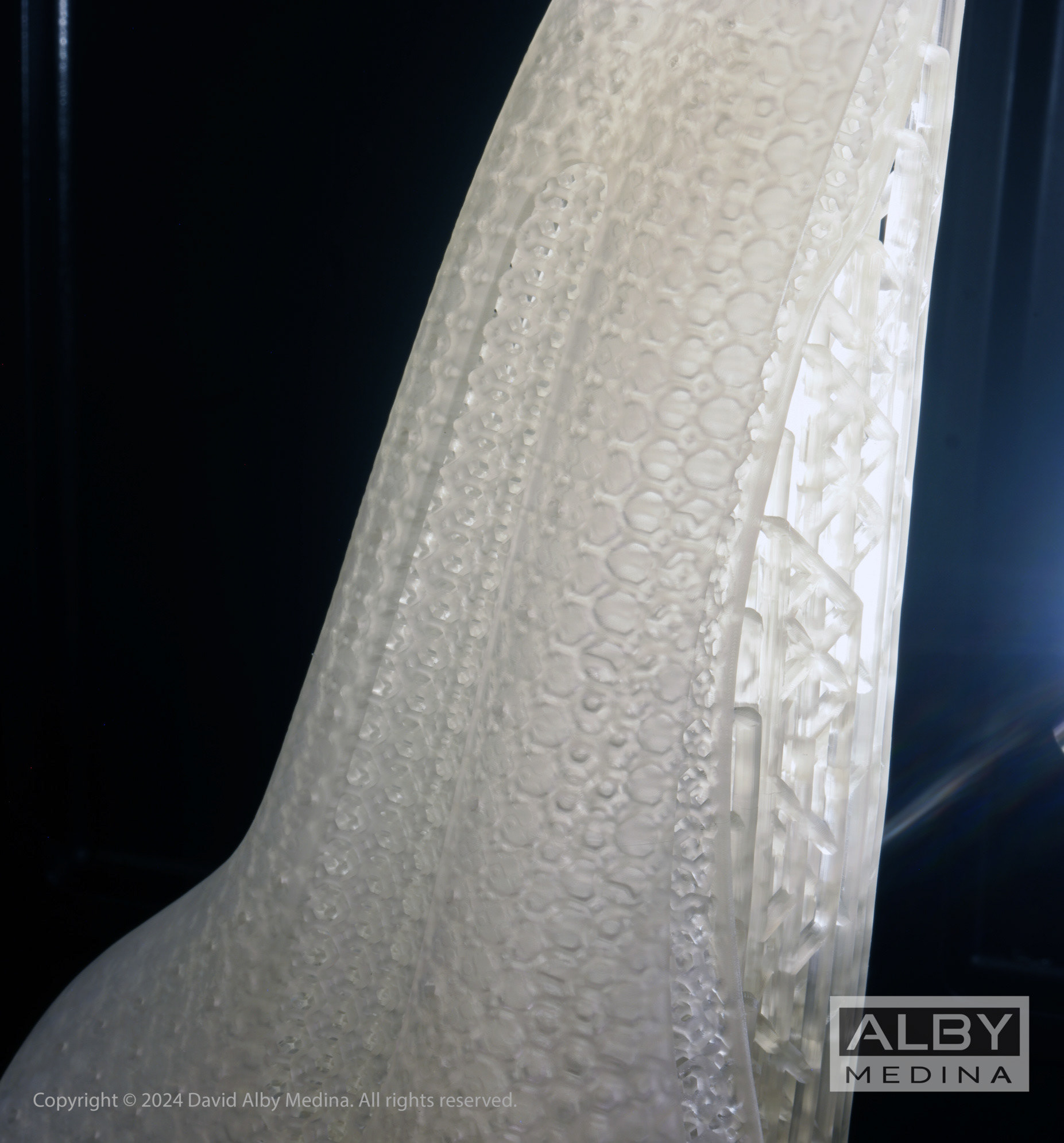
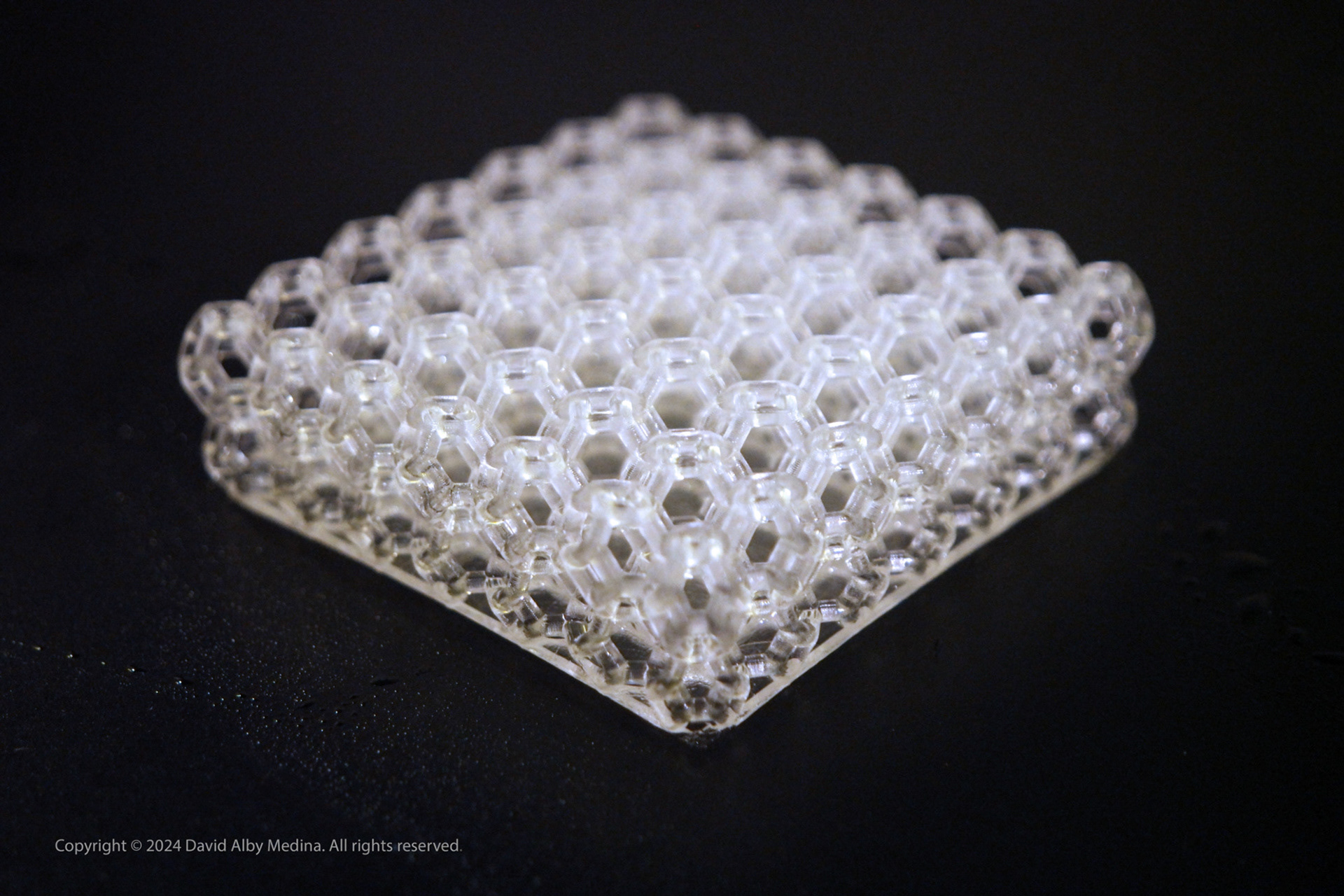
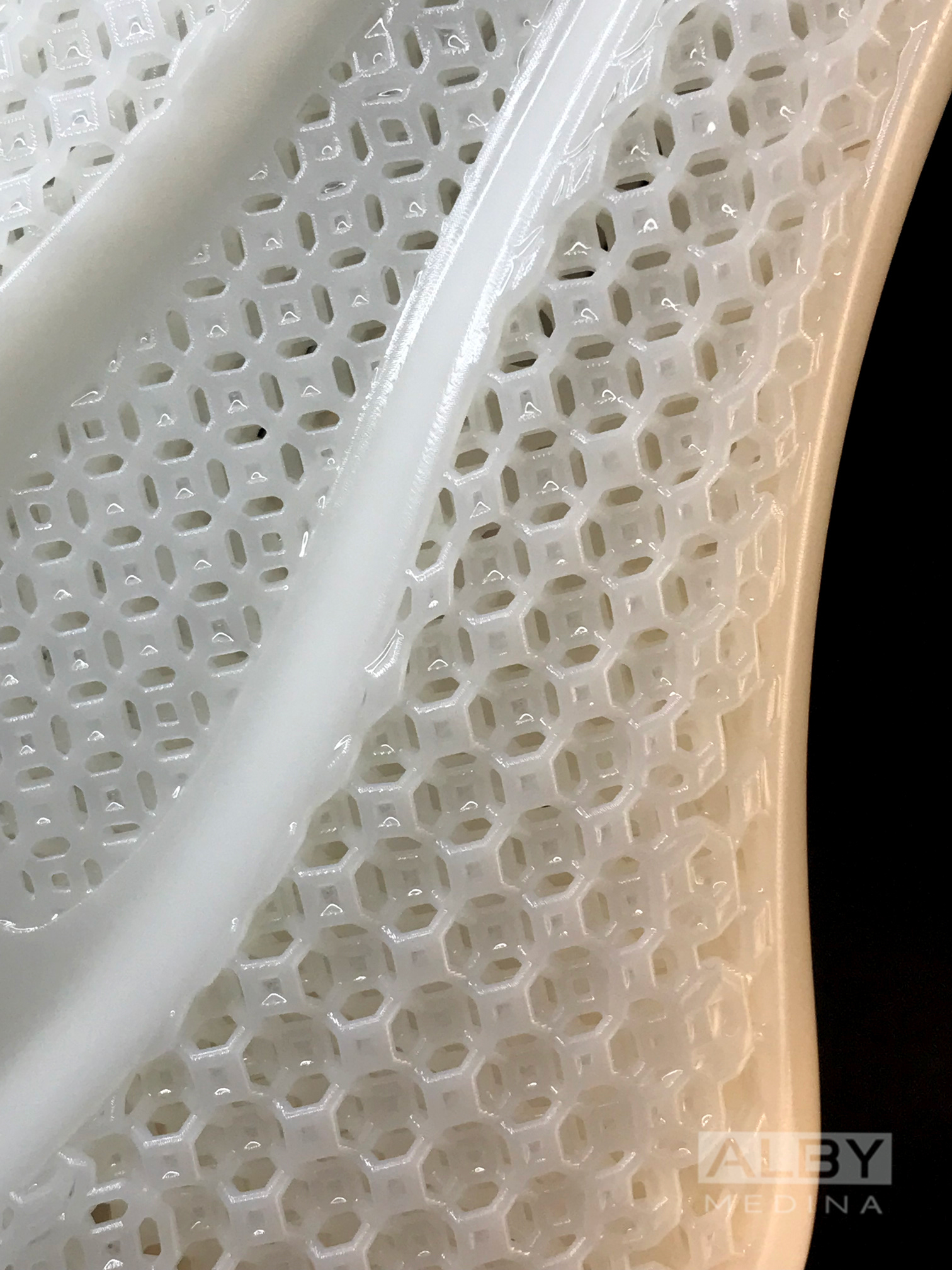
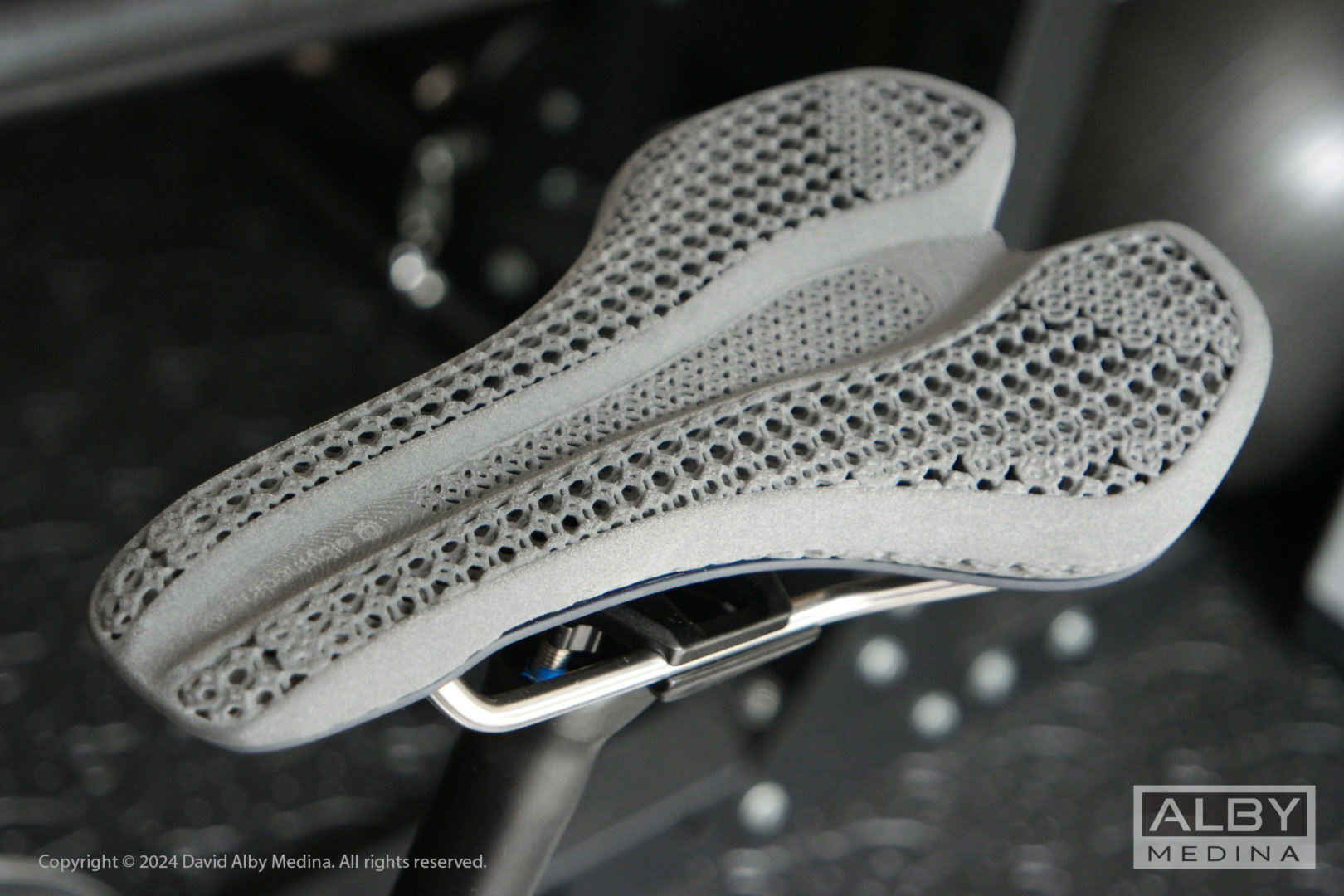
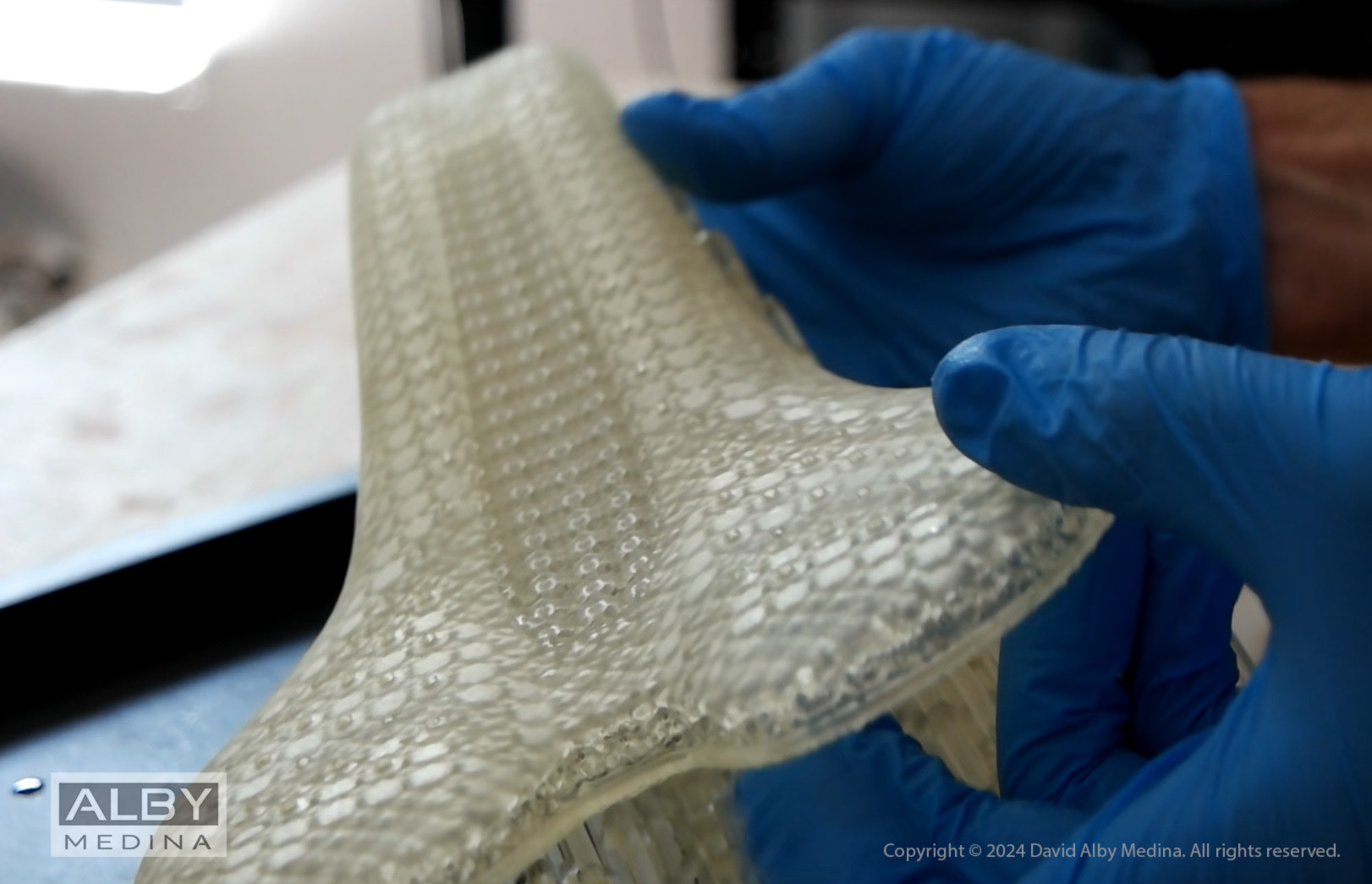
Clear prototyping materials (see image above) allow for more accurate part evaluation. Digital simulations (below) provide early feedback on material behavior before fabrication.
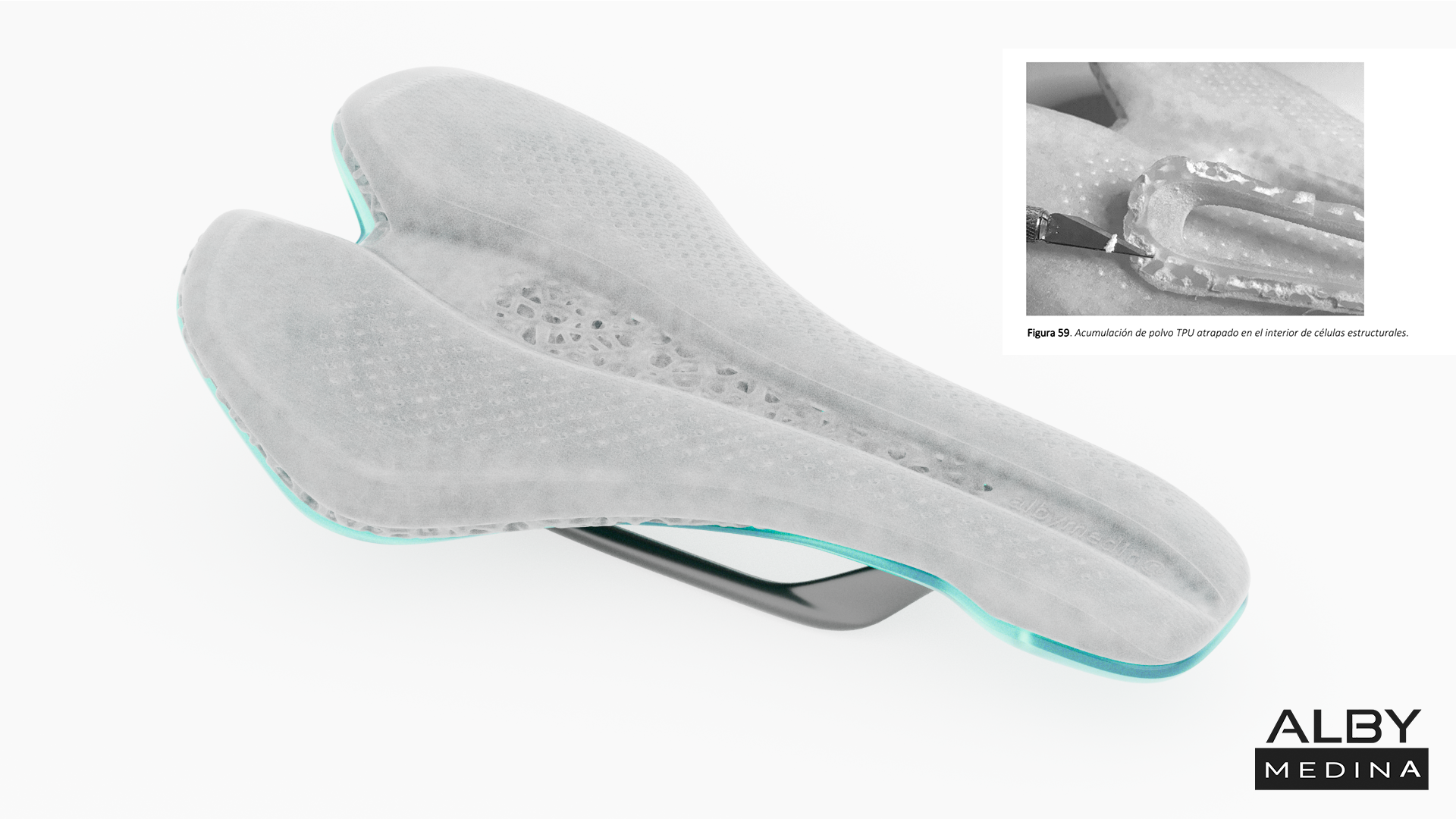

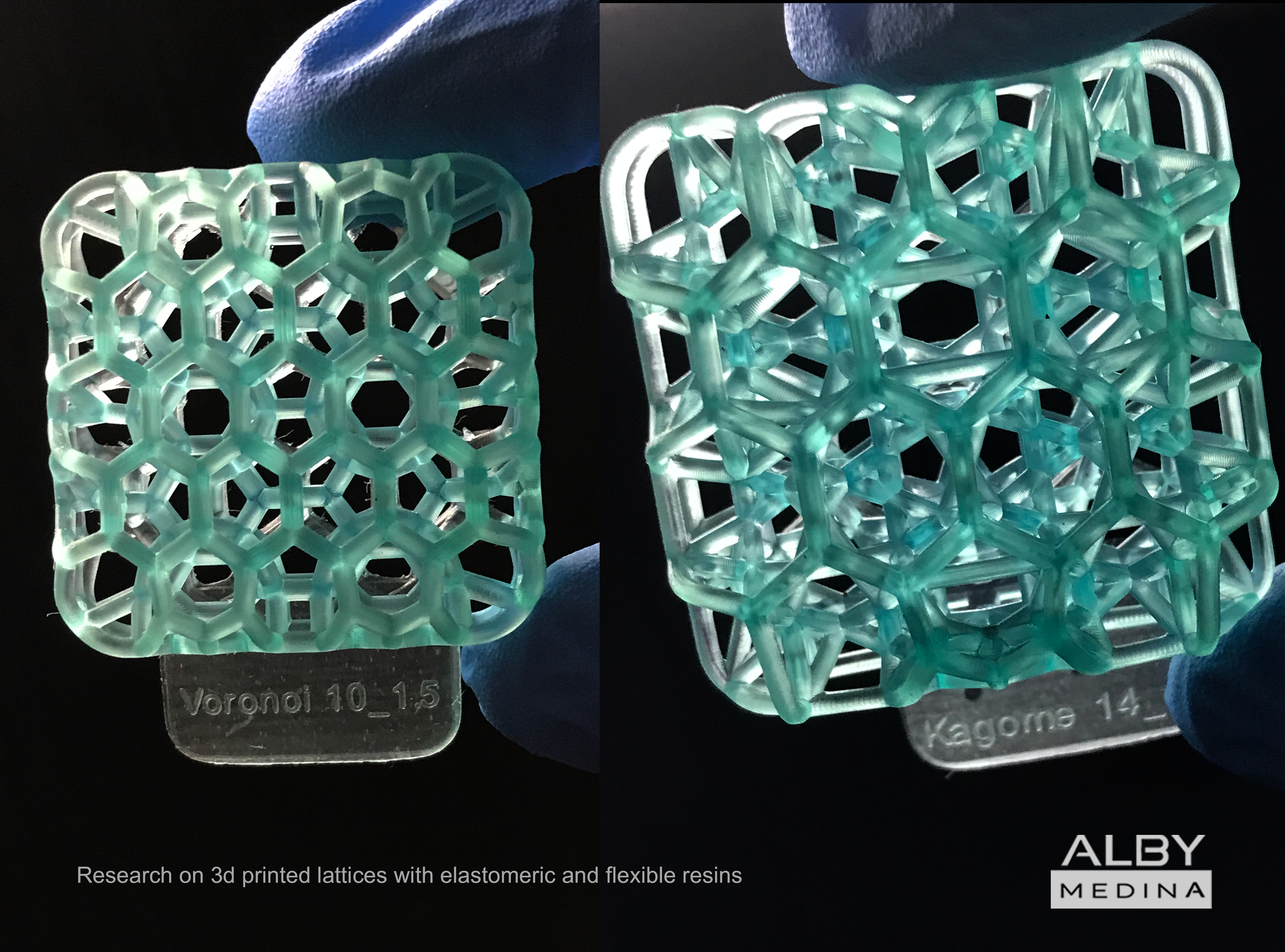
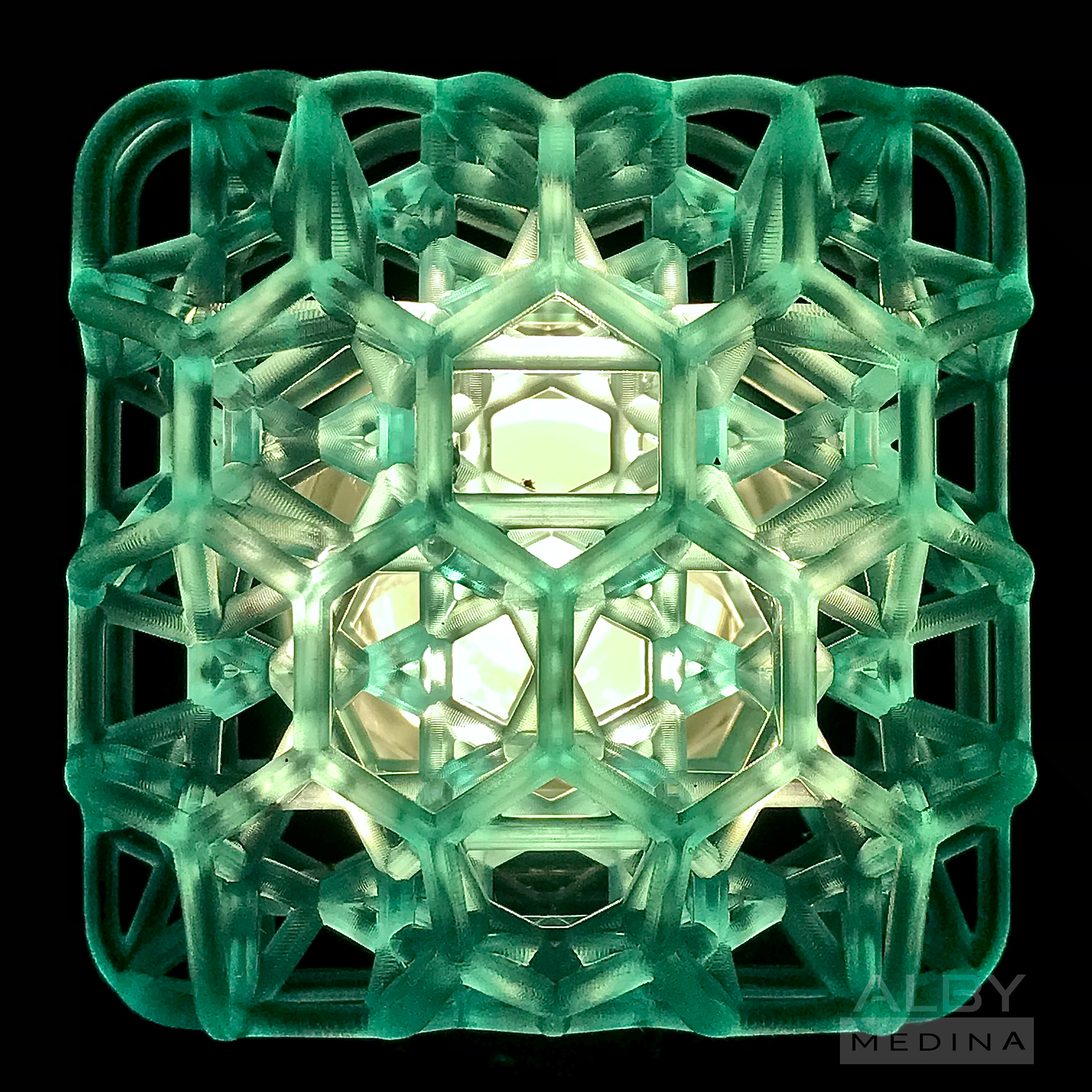