Integrating Hydesign into novel 3d Modeling Workflows
An independent research on accelerating design iterations and improving ergonomic bike saddle padding feasibility
📅 Publication Date: 25.06.2024 | 🔄 Latest Review: 04.08.2025
#3dPrintedBikesaddle #HyDesign
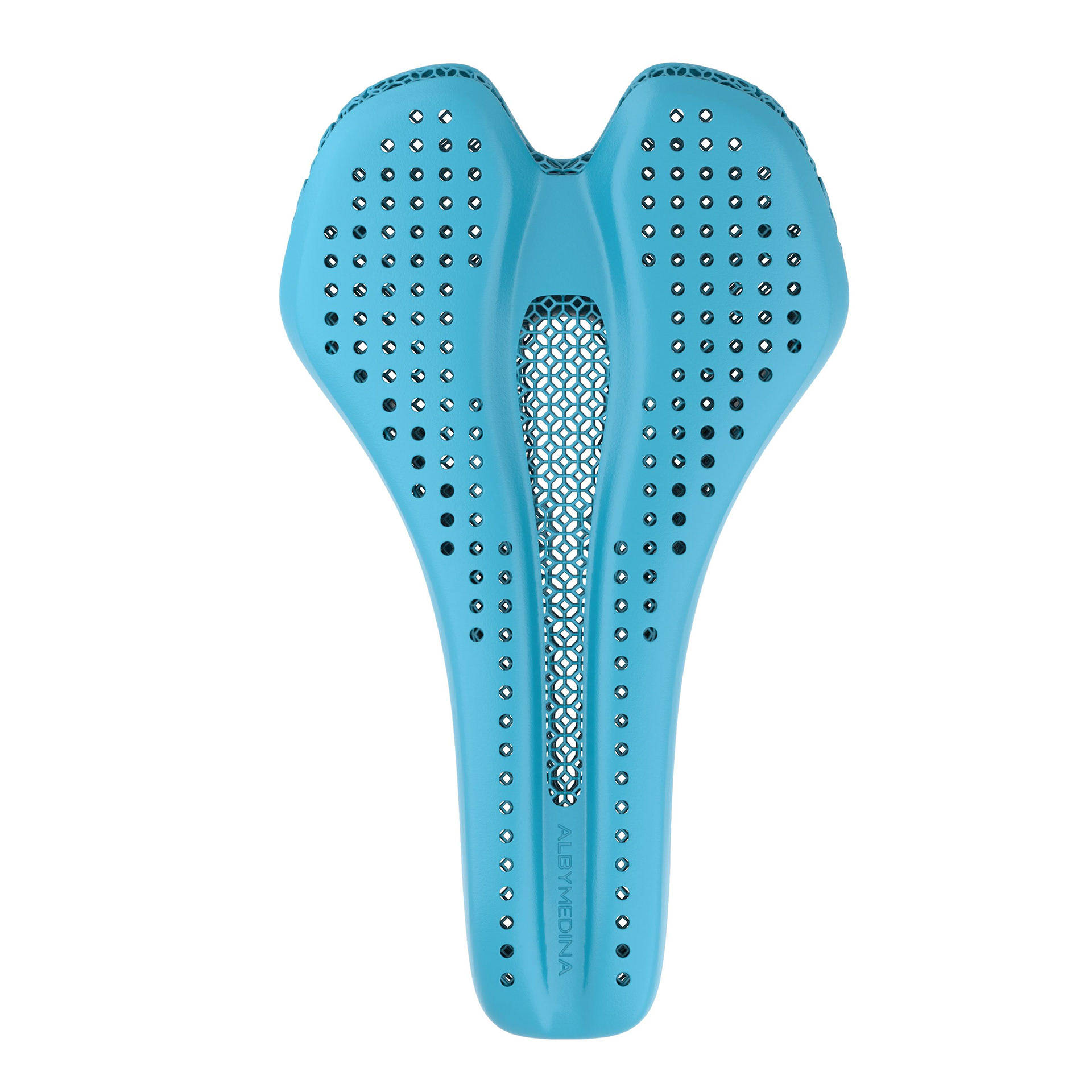
Legal Disclaimer
This website is a showcase of my design work and personal ongoing research. Related technology continue being under development (US Pat. Pend), and international rights may be sought.
Abstract
This project was conducted independently as part of my self-financed research into the challenges of prolonged seated pedaling, particularly within stationary and virtual cycling. The purpose of this case study was to explore how incorporating HyDesign into novel 3D modeling processes could accelerate design iterations and improve the feasibility of producing functional bike saddle padding.
The outcome demonstrated the effective integration of these workflows within a limited budget, contributing valuable insights into the exploration and implementation of novel approaches in 3D concept modeling and prototyping.
​​​​​​​Introduction
This project was conducted independently as a small part of my self-financed research aimed at addressing the challenges of prolonged seated pedaling, particularly in stationary and virtual cycling. The purpose of this case study was to explore how incorporating Hydesign into novel 3D modeling processes could accelerate design iterations and improve the feasibility of bike saddle paddings.
The outcome demonstrated effective integration of these workflows within a contained budget, contributing to the exploration and implementation of novel approaches in 3D concept modeling and prototyping.
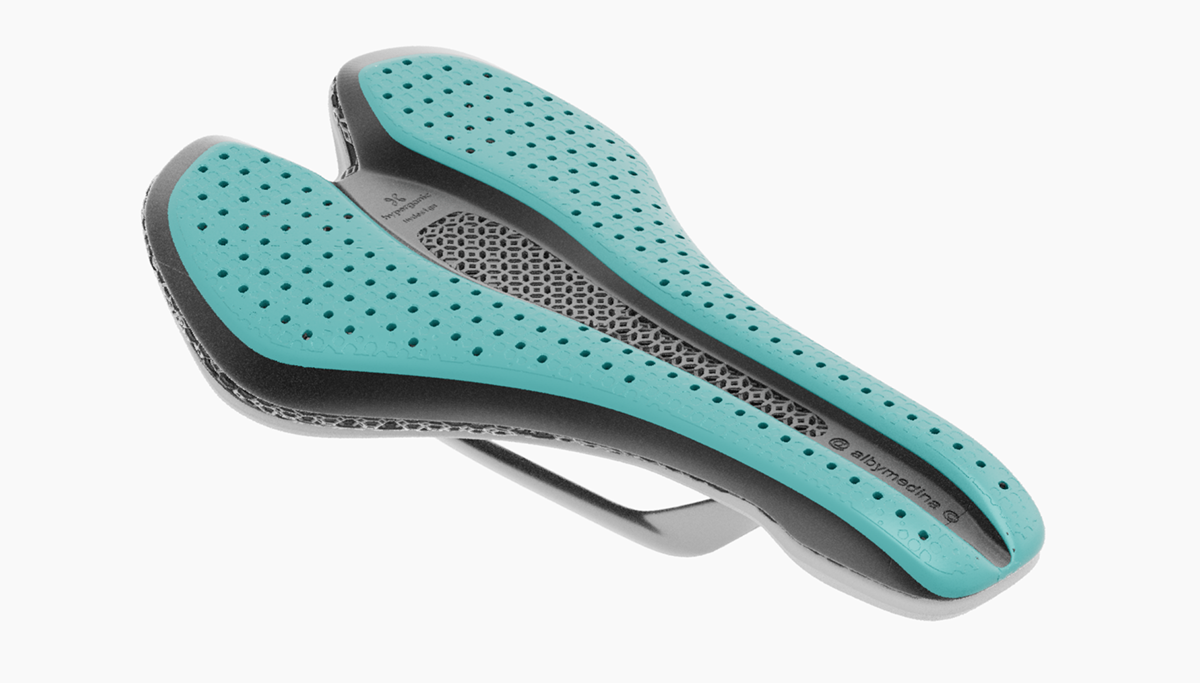
Multi-material saddle. Material Jetting and Powder Bed Fusion additive manuifacturing technologies open endless possibilities in development of custom ergonomic seating applications. Copyright 2024 © David Alby Medina. All Rights Reserved.
Challenge
As a continuation of my Master's Thesis project, I aimed to further optimize functional lattice structures for various saddle designs and materials. My thesis had studied the integration of ergonomic design principles, research methodologies, and novel modeling processes to create a bicycle saddle that enhances comfort and safety during prolonged stationary pedaling.
After completing my studies, I struggled with significant resource and time constraints, leading to a challenging cycle of endless iterations to create functional, feasible designs. The complexity of traditional 3D modeling and limited access to materials compounded these difficulties, while budget constraints restricted potential partnerships for reliable supplies. My goal was to simulate a real-life use case to achieve realistic outcomes despite these limitations.
I tested various implicit modeling and lattice generation tools, but only for short periods due to trial restrictions. Some tools were limited to proprietary materials and fabrication methods; others were not cost-effective or were inaccessible to individual designers. Managing the entire process alone, especially while attempting to create prototypes that approached end-use quality, proved extremely challenging.
Methodology
I developed several design iterations of bike saddle padding by combining traditional polygon modeling with implicit modeling techniques using HyDesign software (refer to Figure 1), alongside lattices from BASF's Lattice Application Discovery Kit. This innovative modeling approach, supported by real-life sample references, enables the creation of detailed functional designs that result in clean models ready for 3D printing without further editing.
I adopted Powder Bed Fusion (HP Multi Jet Fusion) and Vat Photopolymerization (MSLA) additive manufacturing methods, using a broad range of materials such as TPU01 powder, as well as tough and elastomeric resins from the BASF Ultracur3D product line.
​​​​​​​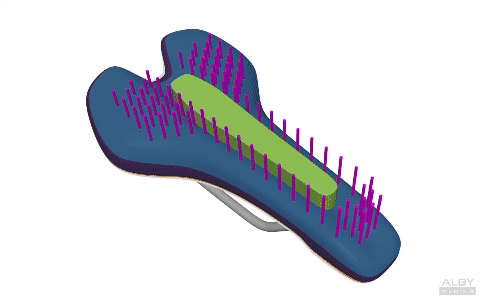
Figure 1. Brief representation of hybrid 3d modeling process, From polygon modeling to Hydesign. Copyright © David Alby Medina. All Rights Reserved.
Compatibility with 3d printing materials and methods
Besides saddle padding embodiments printed in Ultrasint® TPU01 (3D printed by FORWARD AM), I used a variety of UV resin printing materials that I was previously not able to use with satisfactory results during my master's thesis project, so I decided to give them a go. Surprisingly, besides small adjustments in the slicer to secure the 3D printing process, the samples printed fairly well on a consumer-grade 3D printer (Anycubic Photon Mono X).
Generating complex large parts with TPMS and strut-based lattices on consumer-grade 3D printers is not an easy task, requiring a lot of trial and error to achieve reliable and consistent results. It is fair to say that access to generative algorithms that process seamless, supportless lattices greatly contributes to such results.
However, I must admit that I could not properly handle the post-processing of the lattice pads printed in resin, resulting in non-durable parts. Some of the prints did not cure properly, and some required leaving the parts outdoors for a while to get rid of the resin smell.​​​​​​​
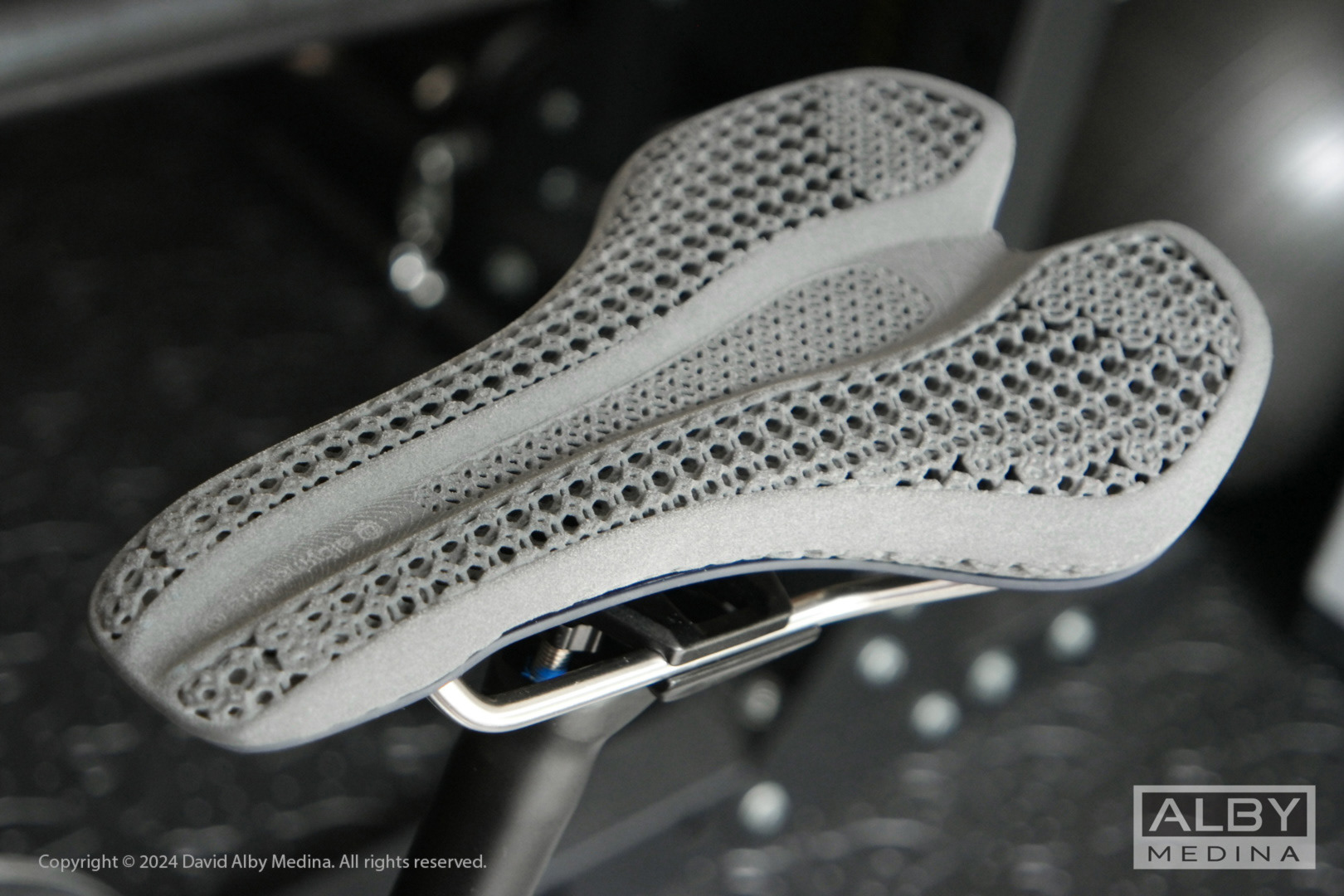
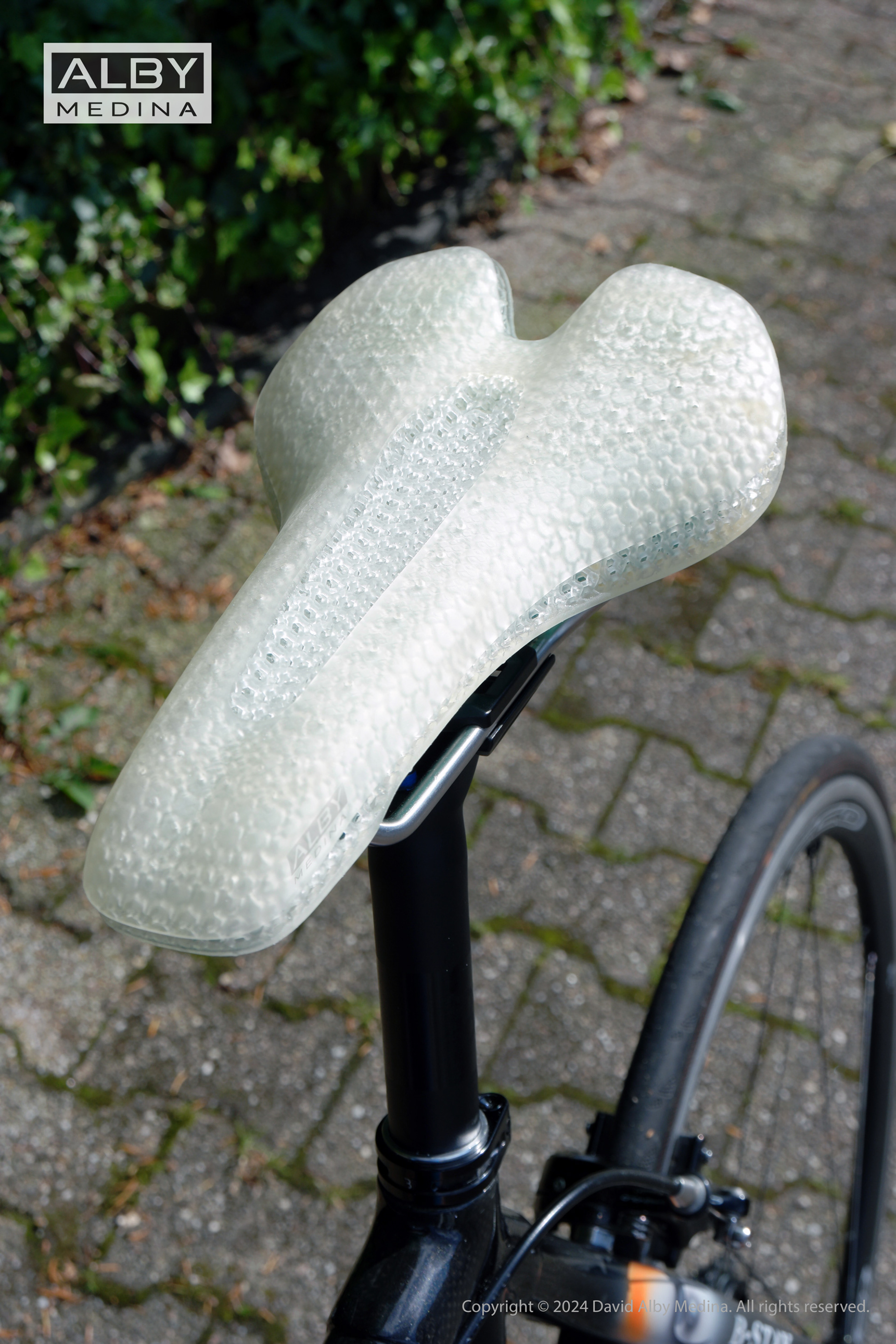
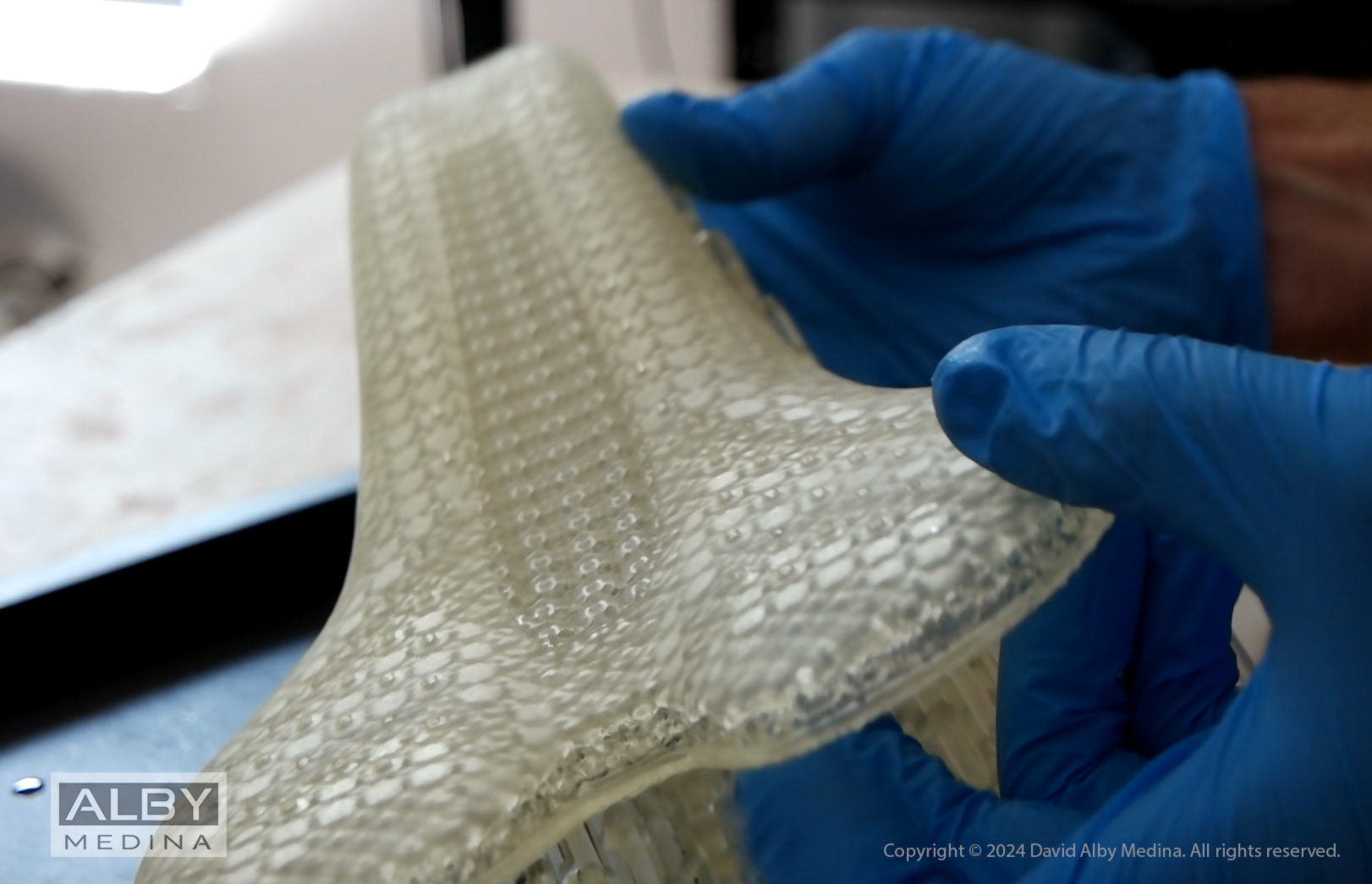
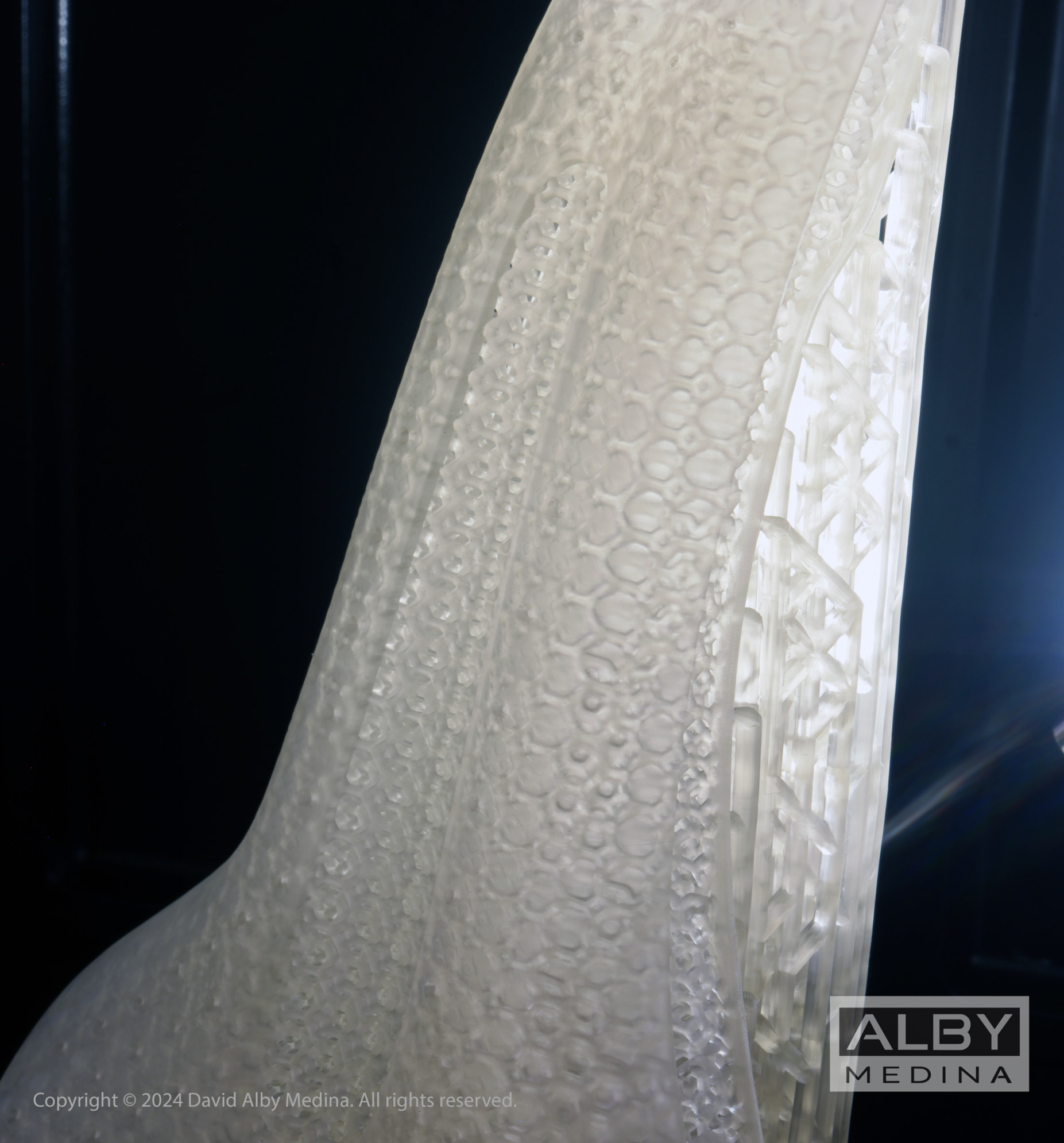
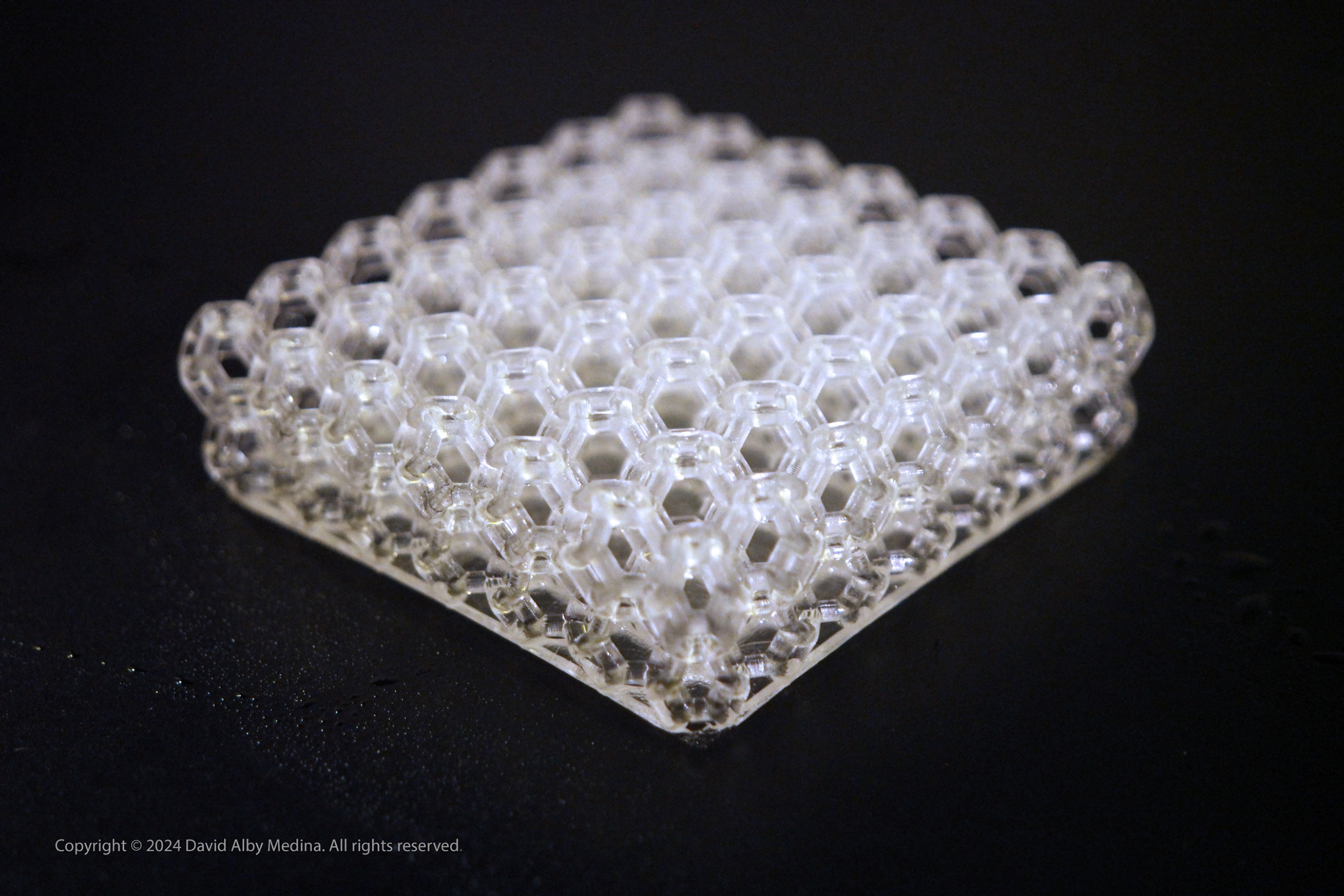
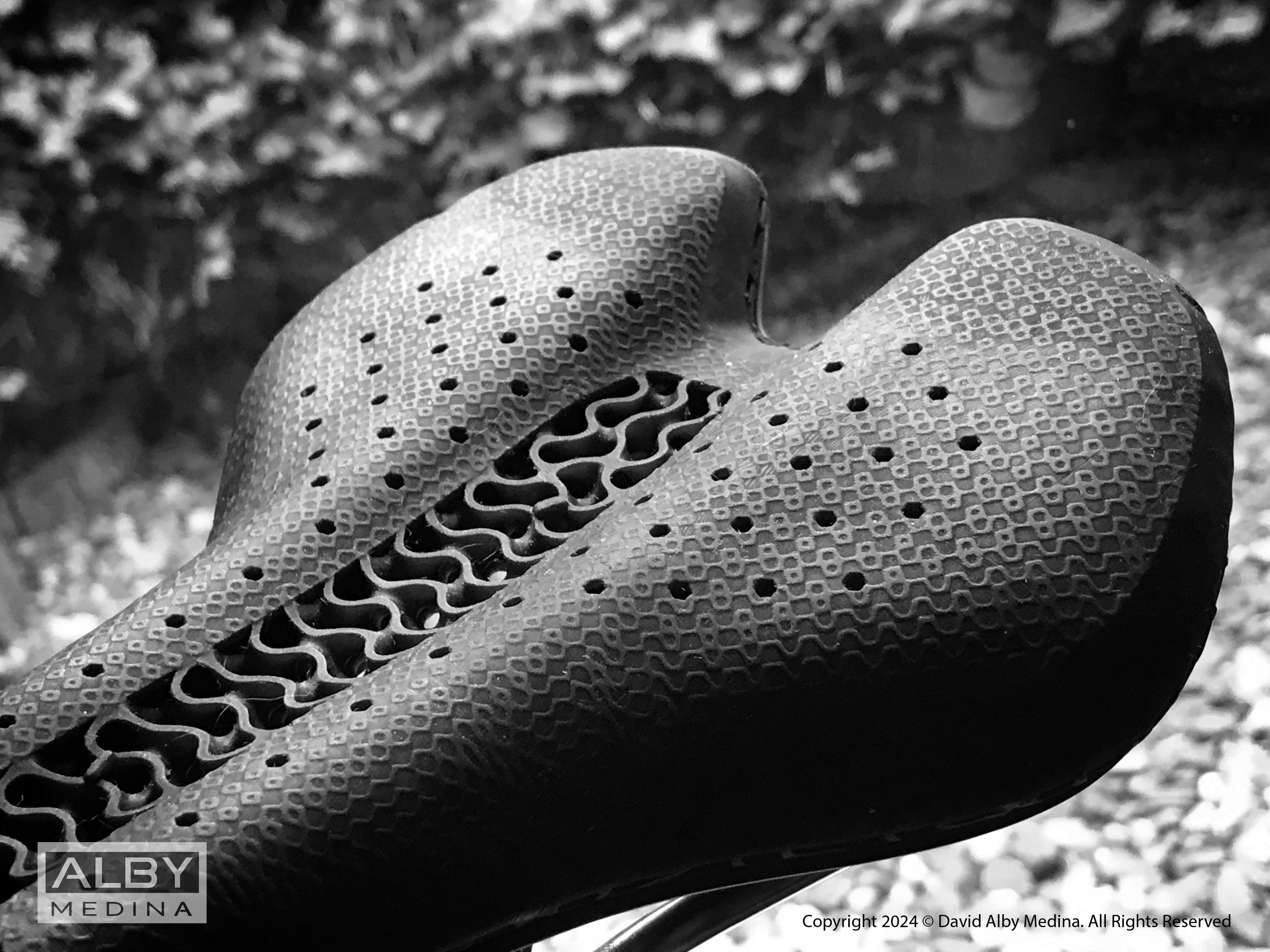
It was found that the biggest challenges we might face from resin printing methods, including closed proprietary methods based on continuous vat photopolymerization, are not about the production itself, but rather the assembly process, when the padding must perfectly conform to the three-dimensional surfaces of the shell body structure.
For that purpose, specific internal processes might be required during the thermal curing cycle, which is when the bonding or, let's say, the complete curing of the two-part resins is achieved. In essence, the forming process of
the padding to be fully adapted onto the shell surface, once bonded usingÂ
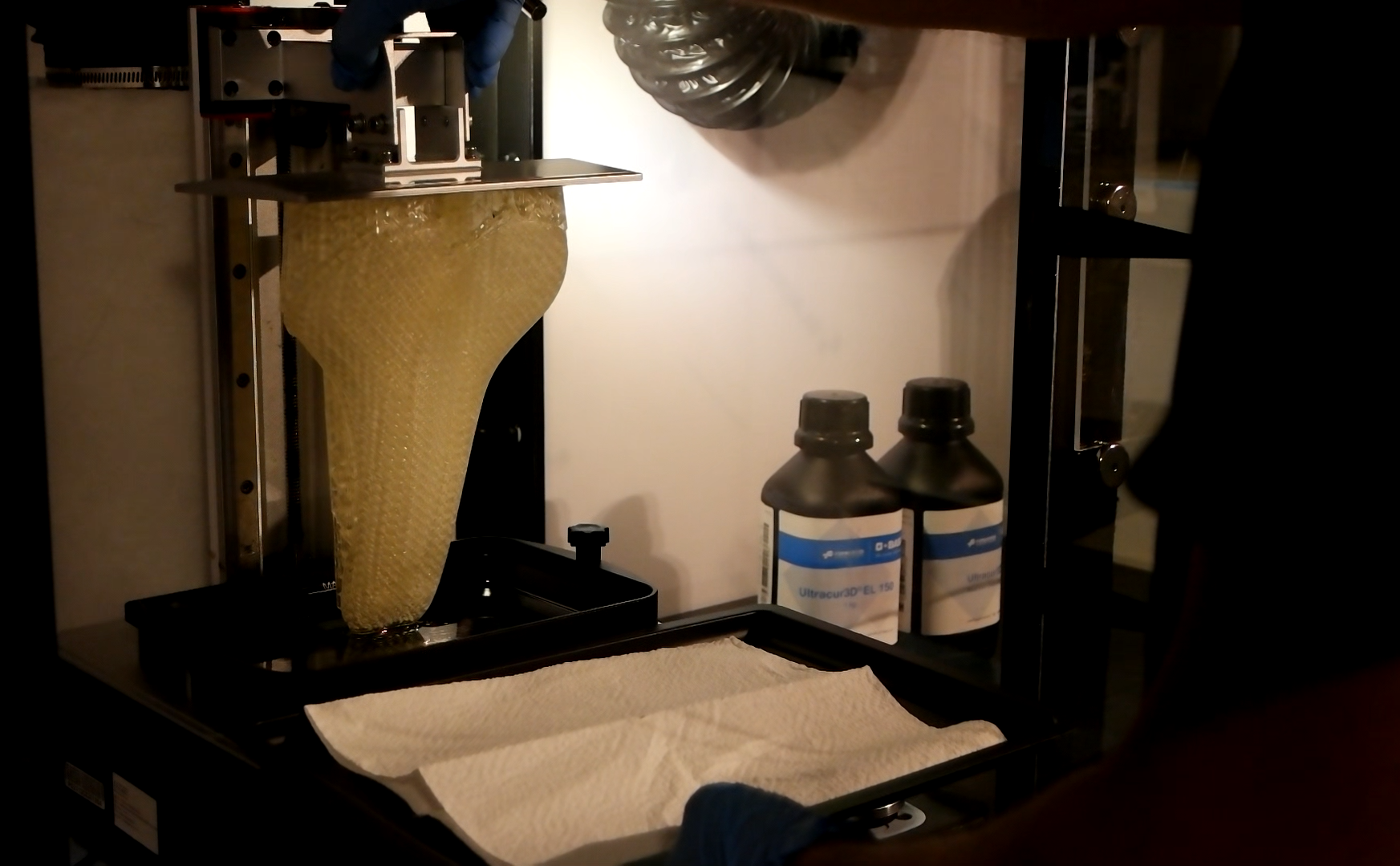
a two-part vulcanizing adhesive, can be (hypothetically) achieved after a final process step consisting of a thermal curing cycle inside a chamber or oven. In summary, while continuous vat photopolymerization presents promising advancements, the process introduces too many challenges, especially when it comes to printing functional parts on a budget.
Pressure mapping. I use pressure mapping data only to get qualitative and visual feedback, due to lack of skills and resources to calibrate the system. In this regard, from the early concept phase prior to this collaboration, I use pressure mapping to support saddle selection (Figure 2). This information helps me to develop the saddle shell structure, while overtime getting a better understanding of the pelvic profile of each individual.
The lattice structures help to improve pressure distribution on the surface of the saddle and minimize maximum stress contact points, providing more comfort to the rider. The aesthetics of the lattices are considered wherever possible.
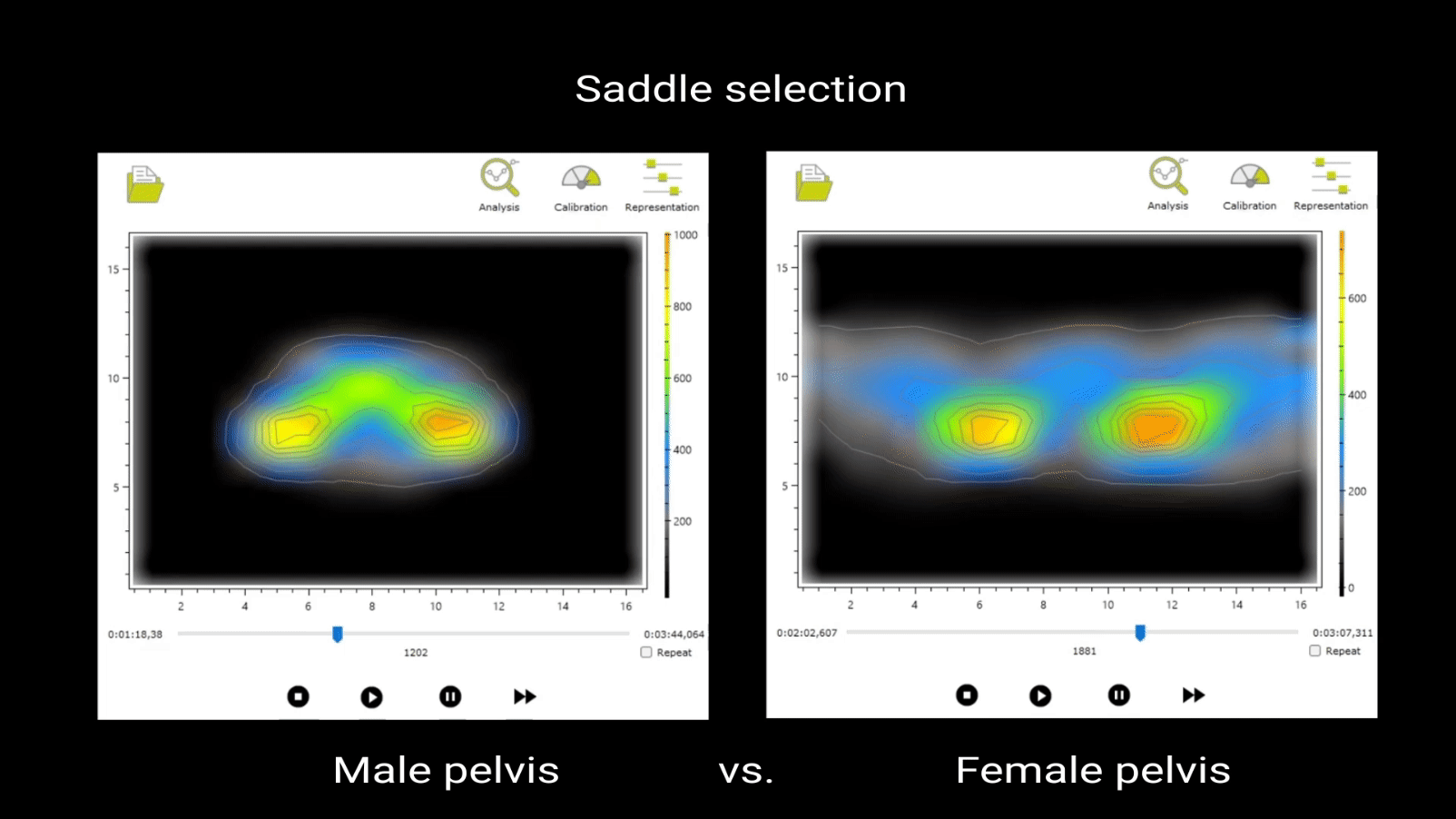
Figure 2. Comparison of pressure mapping data between male and female persons. Software used: Sensing Mat. Copyright 2024 © David Alby Medina. All Rights Reserved.
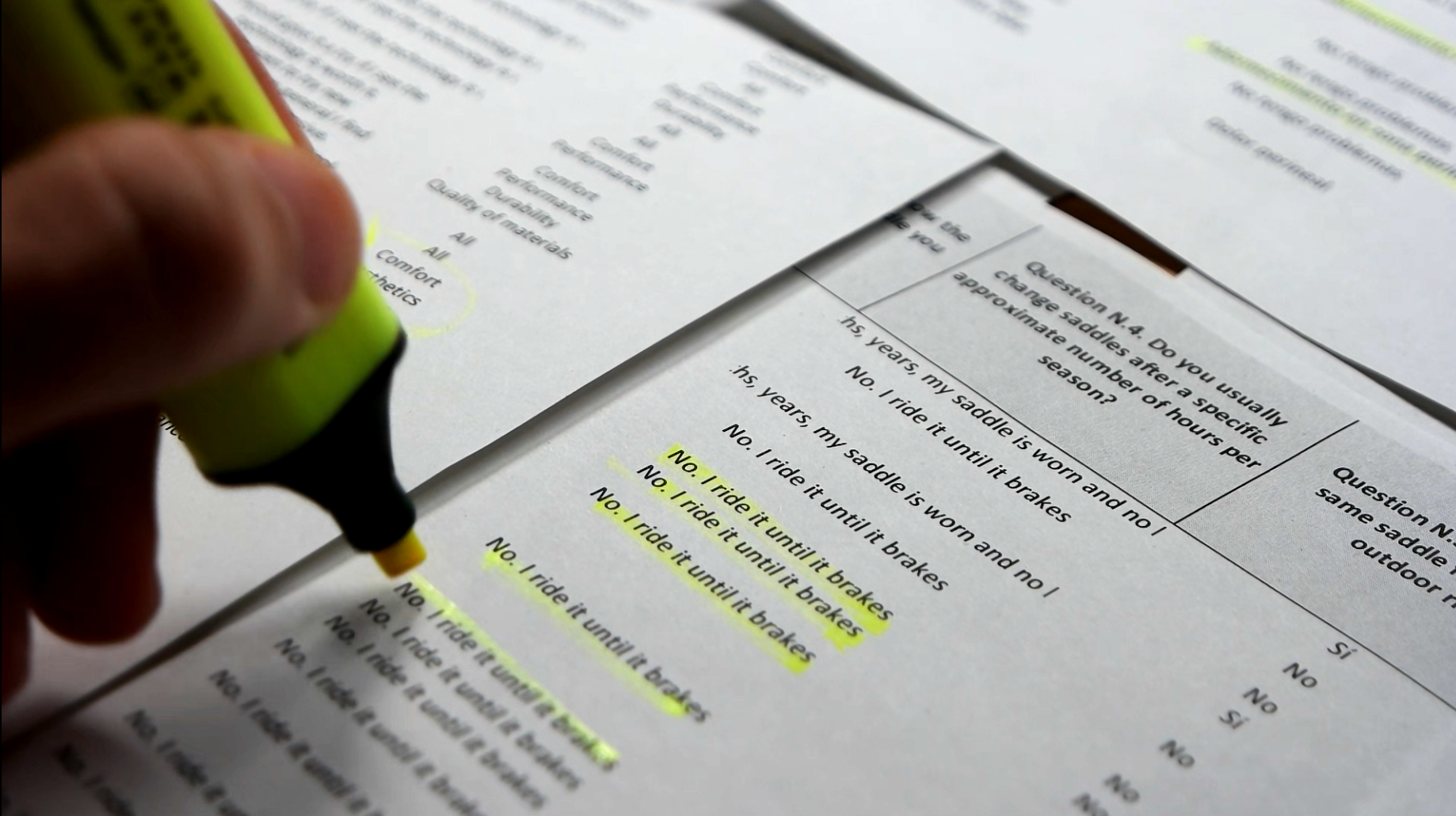
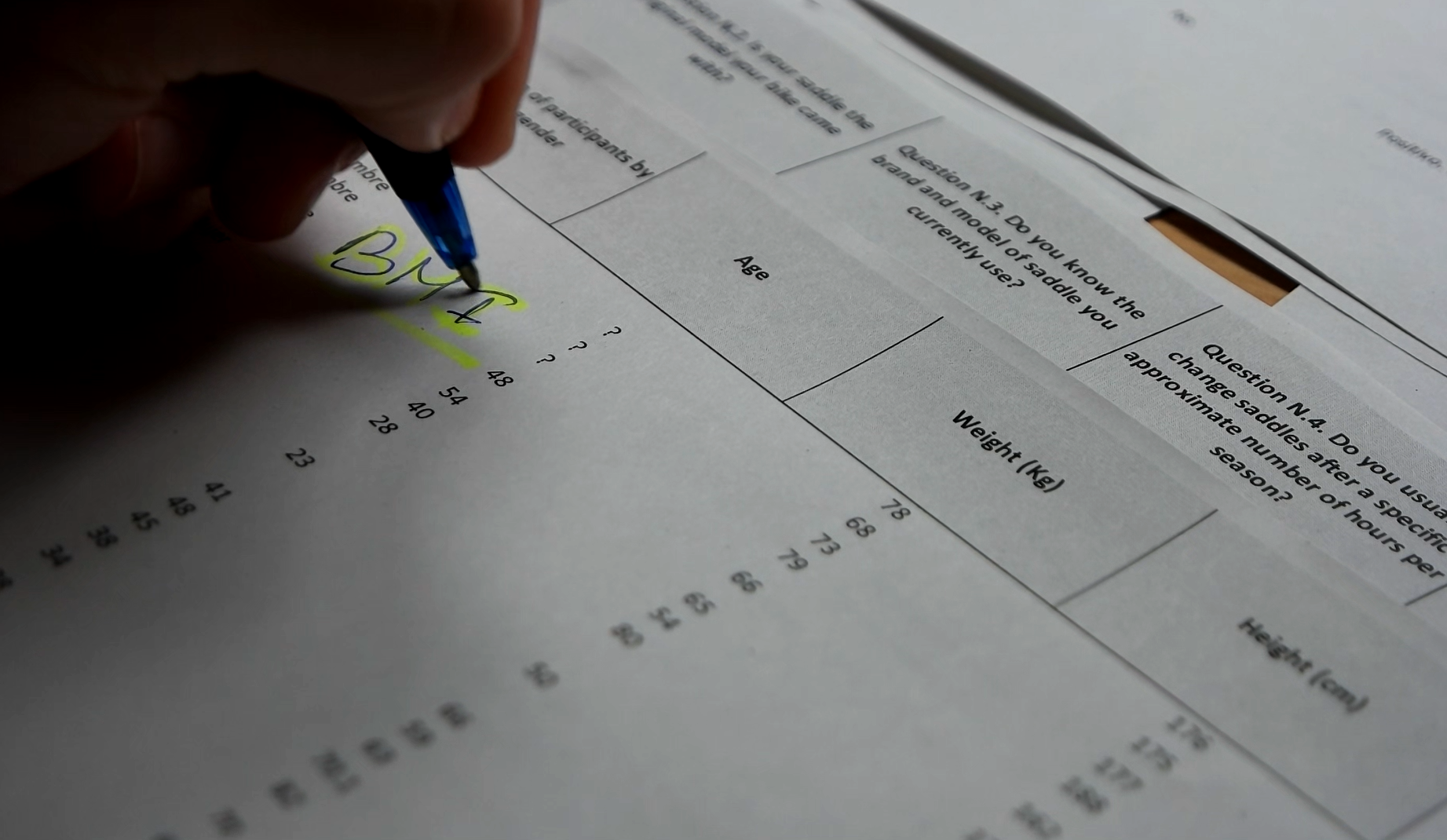
My approach to bike saddle design starts with getting to know the user. Once I have analyzed the collected information, I define the project's direction and begin the ideation phase. In this collaboration project, I continued to prioritize the prototyping cycle (see Figure 3 below). This involved continuously iterating through design phases, testing prototypes, and refining them based on feedback. By emphasizing this iterative process, I was able to efficiently detect and resolve issues, drastically reducing the time required for each iteration cycle. Despite innacuracies resulting from quick design iterations in Hydesign, the models were successfuly printed in resin materials.
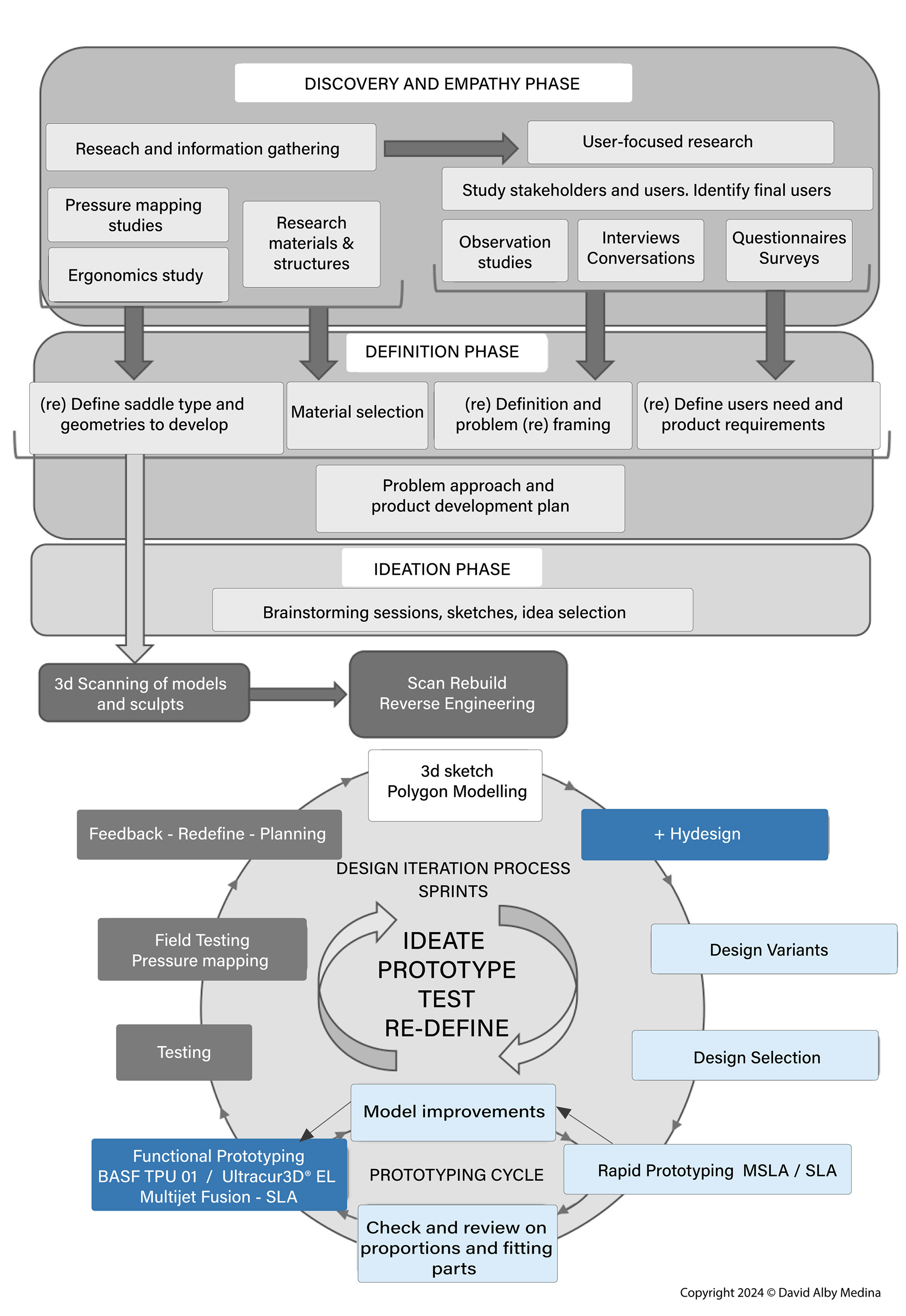
Figure 3. Stages of product development with focus on prototyping cycle.
Copyright © 2024 David Alby Medina.
Copyright © 2024 David Alby Medina.
To accelerate design iterations, I purchased a Lattice Application Discovery Kit along with a library of pre-validated lattice structures available in Hydesign (Figure 4). This significantly streamlined the concept development process for certain design variants.
Since I intended to use a specific lattice type within the saddle padding, the purchase was well worth it in this case. Having a physical sample provided a tangible reference, allowing me to better understand the lattice configuration in real life. This approach proved highly effective as a starting point, particularly since I was still unfamiliar with the material and lattice behavior. It ultimately saved me multiple design iterations.
While I had already selected TPU as a suitable material for my saddle designs, I also experimented with prototyping saddle padding variants using a wide range of resin materials.
Overall, rapid resin printing greatly improved the shapes, proportions, and feasibility of my designs. It enabled testing with functional materials within a relatively short timeframe, helping refine the overall design process.
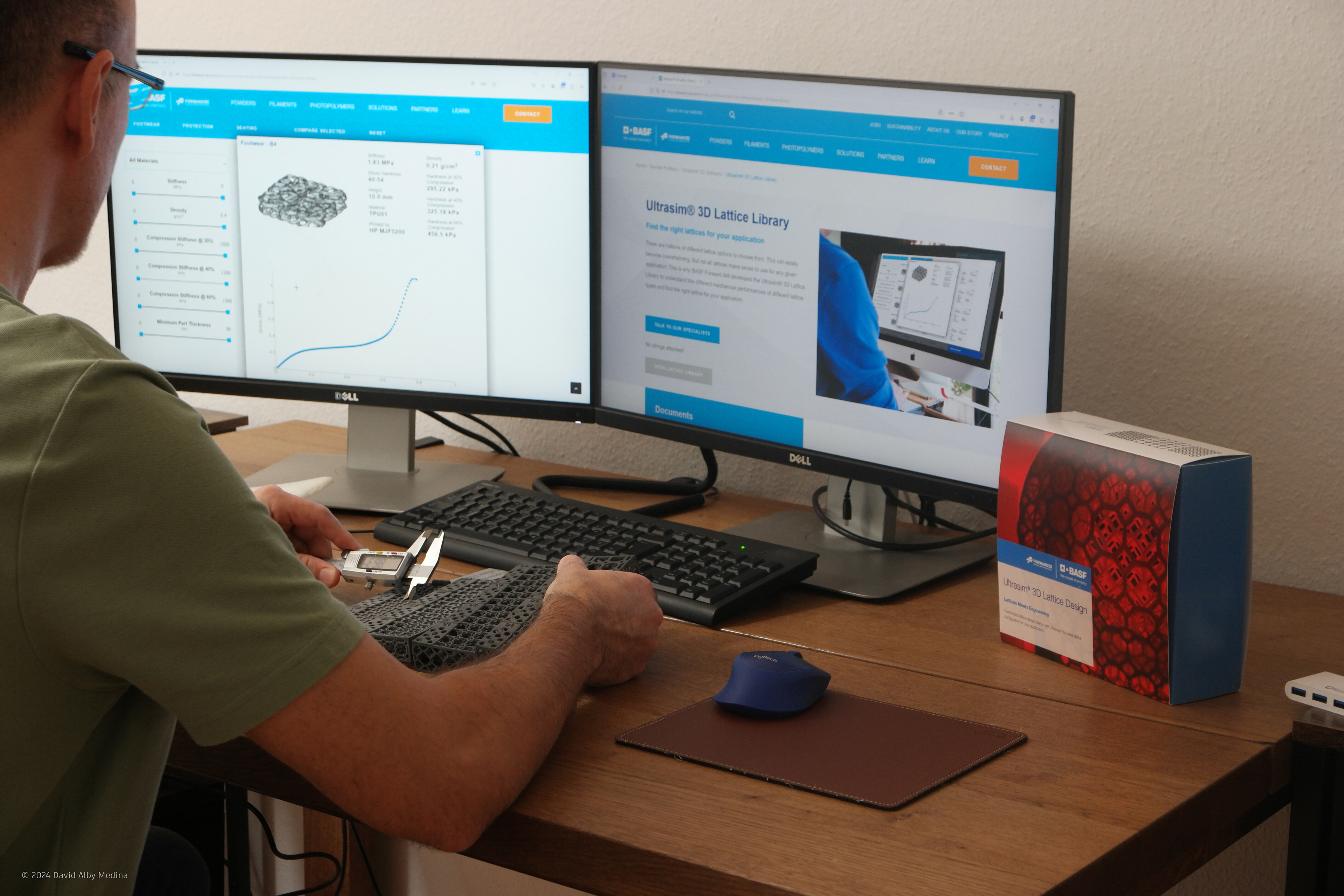
Figure 4. Working with Lattice Application Discovery Kit and Lattice Library. Copyright 2024 © David Alby Medina. All Rights Reserved.
Discussion
In recent years, implicit modeling technology has begun influencing various industries, with the potential to revolutionize current design methods. This was evident during my 2020 design master’s thesis on a saddle project, where I experimented with a combination of implicit and polygon modeling techniques.
Although I had access to advanced modeling software through student licenses, I encountered two primary obstacles:
Although I had access to advanced modeling software through student licenses, I encountered two primary obstacles:
  • Design Feasibility. I could not design practical, strut-based conformal lattices for my saddle pads.
  • Prohibitive Cost. After student licenses expired, softwares became too expensive to maintain.
These challenges restricted further exploration, as the available tools were both complex and costly while failing to address my core design needs. In an increasingly automated work environment, devoting excessive time to such technicalities is often inefficient.
Seeking a more viable and affordable option, I later discovered Hyperganic and their lattice tool, Hydesign. Participating in the beta testing program brought substantial value to my saddle project, particularly due to the Hyperganic team’s user-focused approach and receptiveness to feedback, a dynamic that can be absent when dealing with larger companies.
Hydesign provided a cost-effective and efficient solution for early-stage development, improving padding designs and reducing iteration times. While it has yet to achieve fully seamless conformal lattice generation, it offers a practical compromise by creating functional, pre-validated lattices that rapidly expedite prototyping. This efficiency is crucial under tight deadlines, and the ability to choose different materials and printing methods further streamlines the process.
This experience highlights a broader principle: combining multiple modeling techniques, such as polygon/subdivision, surface, parametric, and implicit modeling, establishes a robust digital toolkit for concept design, particularly for lattice structures. Looking forward, adaptability remains essential as more disruptive, automation-centric tools emerge. The ongoing development and integration of these technologies will shape future workflows, underscoring the importance of staying versatile and receptive to innovative solutions.
Product Evaluation
Context for this Evaluation: The following points are based on my personal experience and general impressions as a participant in the Hydesign beta testing program. This evaluation reflects the state of the software during its pre-release development and does not necessarily represent the full features or performance of the current, publicly available version.
Pros 👍 :
Context for this Evaluation: The following points are based on my personal experience and general impressions as a participant in the Hydesign beta testing program. This evaluation reflects the state of the software during its pre-release development and does not necessarily represent the full features or performance of the current, publicly available version.
Accelerated Workflow: A cost-effective tool for lattice generation that significantly speeds up the design and prototyping process.
Ease of Use: Features a user-friendly interface with a fast learning curve, making advanced techniques accessible.
Creative Freedom: Reduces design iteration times and enhances creativity by minimizing technical complexities and hurdles.
Broad Compatibility: Integrates well with most existing 3D modeling tools (e.g., Blender, FreeCAD).
Democratization of Technology: Removes reliance on expensive software and specialized hardware, making lattice design accessible to more users with consumer-grade 3D printers.
Cloud-Based Computing: Offloads high-demand computing operations to the cloud, eliminating the need for high-performance local hardware.
Material & Supplier Flexibility: Offers versatile material compatibility, supporting project adaptability. It provides both an integrated material marketplace for convenience and the flexibility to use third-party suppliers.
Excellent Support: User-centered customer support with a development team (Hyperganic) that actively listens to and incorporates user feedback.
Extensive Library: Provides a comprehensive library of lattice types to accelerate exploration and design.
Cons 👎 :
Advanced Limitations: During the beta period, the software had technical limitations that required workarounds or specialized support for highly advanced applications.
Fully Conformal Lattice Generation: At the time of testing, the tool did not yet offer fully seamless conformal lattice generation on complex, non-planar surfaces.
Note on Development
A key positive takeaway from the beta experience was the active and responsive development. For example, the initial need for a more extensive lattice library appeared to be addressed in subsequent updates, demonstrating a strong commitment to user-driven improvement.
_________________________________________________________________________
Important Notice
This is a self financed publication, not an sponsored publication.
The content in this publication is part of my self-financed research focused on addressing the challenges of prolonged seated pedaling, particularly during stationary and virtual cycling scenarios. Resources have been provided by myself, excepting Hydesign license due to beta testing, as well as printed saddle pads in TPU01 from BASF Forward AM. Hydesign provided a beta testing license and user feedback without any participation or rights over in the design and development of the saddle.Â
The content in this publication is part of my self-financed research focused on addressing the challenges of prolonged seated pedaling, particularly during stationary and virtual cycling scenarios. Resources have been provided by myself, excepting Hydesign license due to beta testing, as well as printed saddle pads in TPU01 from BASF Forward AM. Hydesign provided a beta testing license and user feedback without any participation or rights over in the design and development of the saddle.Â
Copyright Notice
All images and content, including all saddle-related material showcased in the video published by Hyperganic, are under the authorship and private property rights of David Alby Medina, except for the video editing, third-party logos, and turnaround visualization of the lattice padding. These elements are included solely to acknowledge collaborations. All designs presented in any format remain under David Alby Medina's full intellectual property rights. Unauthorized distribution, modification, or commercialization of this content, in whole or in part, is strictly prohibited without explicit written consent. Any violation may result in legal action.
Legal Disclaimer
This website is a showcase of my design work and personal ongoing research. Related technology continue being under development (US Pat. Pend), and international rights may be sought.